Основы бережливого производства: lean-инструменты и виды потерь
Бизнес и эффективность
ИТ в промышленности
25 марта 2024
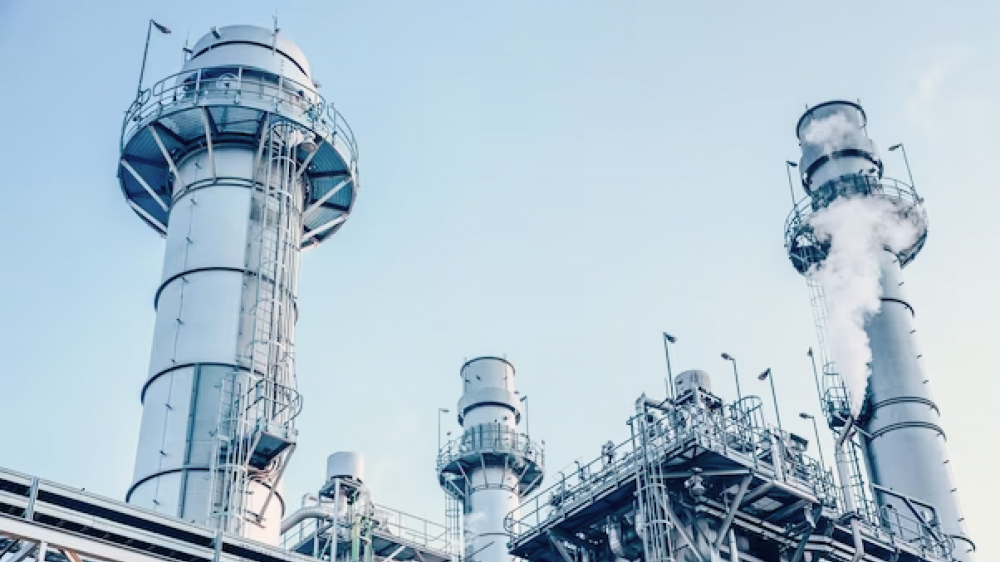
Содержание
Что такое бережливое производство
Бережливое производство, или lean production (lean-технологии) — концепция управления процессами, направленная на сокращение потерь и повышение качества продукта, сервиса.
Первые шаги в улучшениях начал делать Генри Форд в 1919 году. А уже в 1946-ом Эдвард Деминг обучал японцев статистическому управлению качеством. Философия бережливого производства зародилась в Японии, когда один из руководителей Toyota — Тайити Оно — создал новую модель управления и успешно внедрил ее в компании. Он выделил три фактора, которые приводят к убыткам:
- Muda, или потери (отходы, мусор) — деятельность, которая не несет ценности. Хорошим примером будет эпизод из мультфильма «Двенадцать подвигов Астерикса», когда герою нужно было получить разрешение и пройти разные инстанции и бюрократические проволочки. В ходе процесса он видит, как из-за сложной системы и бесполезных действий все начинают сходить с ума.
- Mura, или неравномерность — нестабильная ситуация на производстве. Например, разрозненный график поставок, недостаточное количество сотрудников или оборудования.
- Muri, или перегрузка — перенапряжение работников или изнашивание оборудования из-за интенсивной работы. Это ведет к неравномерности, а значит — к простоям и издержкам.
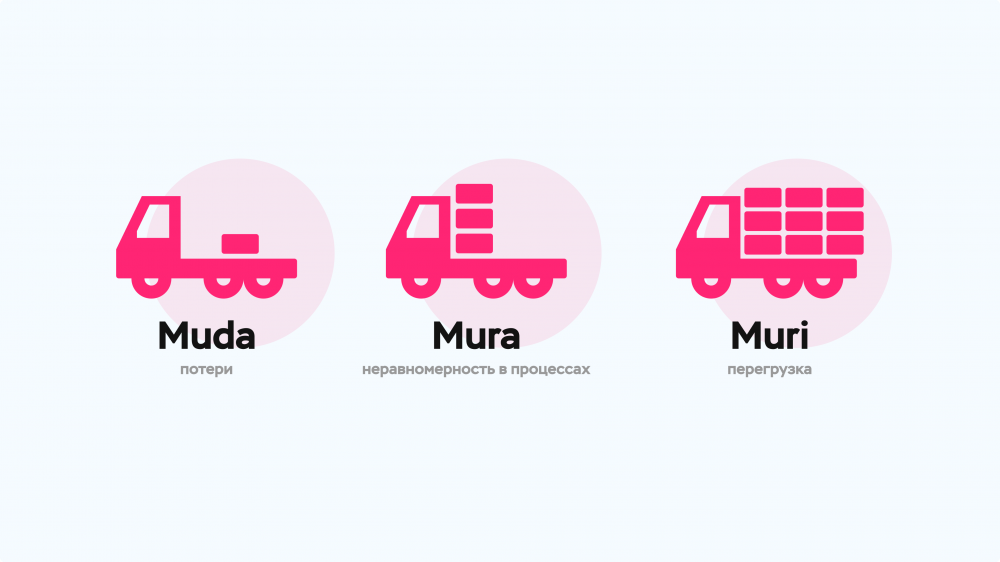
Цели бережливого производства: стабилизация бизнес-процессов, создание регламентов, уменьшение потерь и внедрение улучшений. Избавление от лишнего должно повышать эффективность и качество, снижать траты, упрощать обслуживание оборудования и обеспечивать экономию.
Идеи Тайити Оно успешно показали себя на производстве и концепцию начали использовать во всем мире. В 1988 году появился термин lean. Его ввел и распространил в Европе и Северной Америке Джон Кравчик.
1992 — создание производственной системы Toyota Supplier Support Center (TSSC) и начало широкого распространения ее в США и Европе.
В 2000 году лин пришел в Россию и начал развитие не только в компаниях, но и на государственном уровне. Существует ГОСТ Р 56404 по бережливому производству, в котором прописана суть концепции и то, как ее следует применять в различных отраслях:
- Стандарты работы.
- Организация рабочего места.
- Работа с картой создания ценности, методом быстрой перекладки, защитой от недочетов и другими инструментами.
Принципы бережливого производства
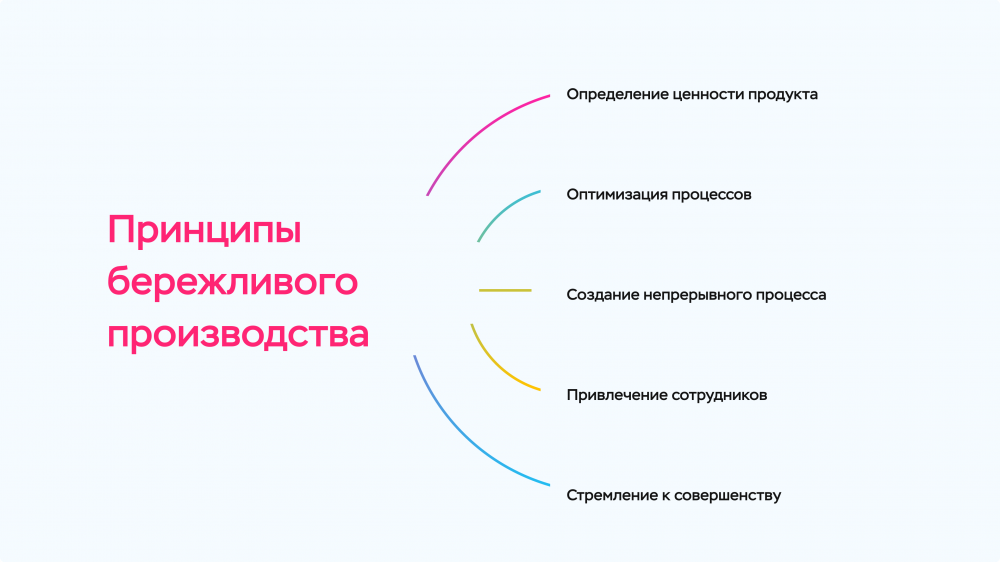
Пять основных принципов бережливого производства:
- Определение ценности продукта. Сначала нужно понять, что является важным и существенным для конечного потребителя и каким он хочет видеть товар. Это поможет сосредоточиться на основных процессах, создавать продукты с высоким спросом, качественный сервис, а также сокращать лишние запасы.
- Оптимизация процессов для устранения потерь. Нужно проанализировать все этапы производства, чтобы вовремя избавиться от излишков запасов сырья, устранить простои оборудования, снизить затраты и внедрить улучшения.
- Создание непрерывного процесса — равномерный поток от запроса клиента до получения продукта. Например, поиск возможностей для оптимизации производства, внедрение новых технологий, адаптация к требованиям рынка и желаниям потребителей.
- Привлечение сотрудников. Люди, которые непосредственно участвуют в процессе, видят слабые места. Персонал должен быть заинтересован в том, чтобы предлагать идеи для решения проблем и принимать активное участие в реализации изменений. Так сотрудники почувствуют собственную значимость для компании.
- Стремление к совершенству. Конечно, невозможно добиться идеала, но нужно ставить такую цель, непрерывно улучшая процессы и продукты. Максимального эффекта можно будет добиться, если выявлять потери и устранять их на постоянной основе.
Плюсы и минусы философии lean
Любая система управления имеет преимущества и недостатки, поэтому нужно учитывать особенности лин перед тем, как его внедрять.
Преимущества
- Снижение потерь. Благодаря устранению избытка и оптимизации производства, компании экономят деньги и время.
- Увеличение производительности. Оптимизация процессов и уменьшение потерь повышает эффективность бережливого производства.
- Забота об окружающей среде. Снижение уровня отходов и эффективное использование ресурсов помогает снизить негативное воздействие на экологию.
- Экономия места. Продуманная организация рабочих мест позволяет сэкономить на аренде помещений и обустроить склад.
- Контроль качества на каждом этапе разработки продукта. Это помогает снизить количество брака и простоя.
- Участие сотрудников. Благодаря поддержке и стимулированию инициативы персонала, каждый участник вносит свой вклад в улучшение процессов и предлагает новые идеи.
- Увеличение уровня лояльности клиентов. Высокое качество продукции, сокращение издержек, работа с ценовой политикой помогают компаниям удерживать потребителей.
- Рост выручки через производство востребованной продукции и уменьшения расходов.
Недостатки
- Зависимость от поставщиков. Проблемы с поставками могут сильно отразиться на репутации бренда и качестве товара. Нужно предусмотреть возможные риски и согласовать процессы с поставщиками.
- Большие затраты. Начальные инвестиции на демонтаж, переоборудование рабочего пространства и обучение.
- Сопротивление сотрудников. Сложности с персоналом из-за того, что люди не понимают преимущества системы или не заинтересованы участвовать в процессе.
- Сложность внедрения. Изменения внутренней культуры и структуры компании увеличивают нагрузку на сотрудников и требуют от руководства дополнительного внимания и контроля.
- Потеря фокуса на качестве. Активное устранение отходов и упрощение производства может приведет к снижению качества продукции.
Виды потерь в бережливом производстве
Определяют восемь видов потерь в бережливом производстве.
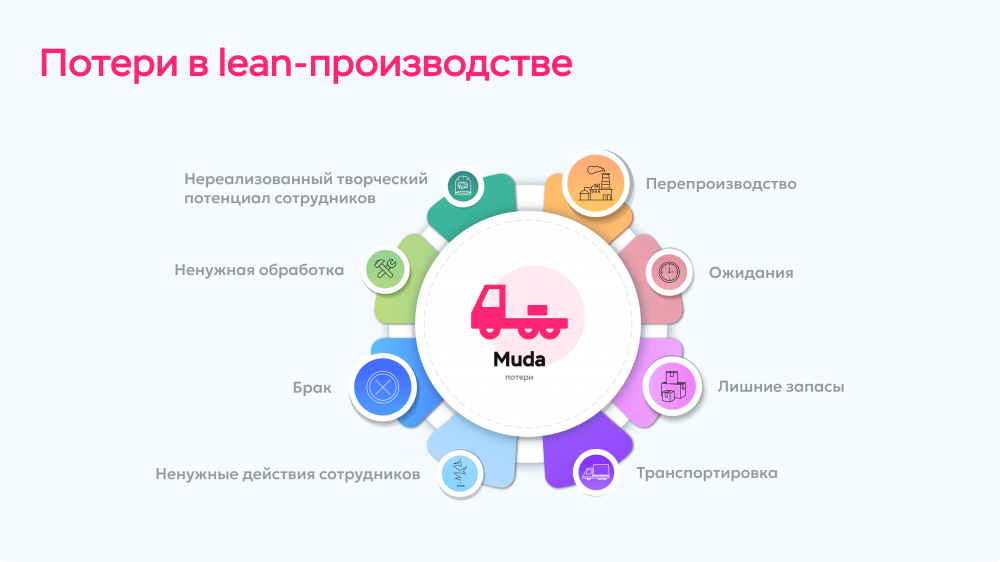
Перепроизводство
Избыток товаров увеличивает затраты на их хранение и материалы. Например, компания произвела 10 000 товаров, при этом реальный спрос составляет всего 5 000. Это приведет к избыточному запасу продукции на складе и дополнительным затратам на его обслуживание.
Ожидания
Потери, связанные с простоем оборудования и ожиданием ресурсов от поставщика или службы доставки. Например, станок на линии производства останавливается из-за отсутствия материалов для упаковки товара.
Лишние запасы
Приобретение и хранение дополнительных материалов является незавершенным производством. То есть замороженные активы, которые не используются в бизнесе. Например, компания купила запасные детали и не учла реальные потребности производства. Резерв занимает место на складе, хотя эти деньги можно было инвестировать для более приоритетных задач.
Транспортировка
Сложности, которые возникают при перевозке товаров или материалов, увеличивают риски: повреждение деталей, долгая доставка, недостаточное количество машин или перегруз транспортного средства.
Ненужные действия сотрудников
Лишние перемещения по офису или действия в процессе производства, чтобы найти конкретную вещь или передать документы в другой отдел, отнимают много времени и повышают стоимость одной единицы товара.
Брак
Дефекты на производстве или ошибки из-за человеческого фактора увеличивают расходы и издержки. Например, сотрудник получил техническое задание, но руководитель в спешке забыл дать комментарии к некоторым требованиям. Итог — изделие нужно изготовить заново.
Ненужная обработка
Лишние этапы создания продукта приводят к потерям. К примеру, на заводе по производству мебели после фрезеровки столешницы дополнительно проводят полировку. Но это не требуется для достижения нужного качества товара. Лишняя обработка увеличивает время и тратит ресурсы.
Нереализованный творческий потенциал сотрудников
Проблема появляется, когда руководство не прислушивается к идеям персонала или выставляет жесткие рамки с помощью правил и должностных обязанностей. Но личные качества, знания и навыки работника помогают ему увидеть недочеты на своем рабочем месте и придумать уникальное решение.
Чтобы раскрыть человеческий потенциал и при этом минимизировать потери, мы разработали для добывающего холдинга сервис реализации инициатив.
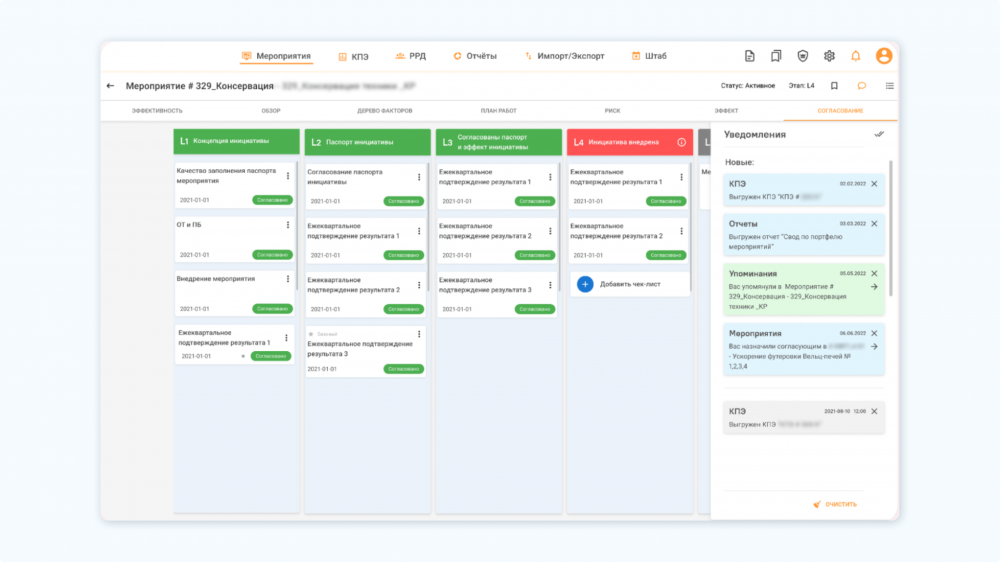
Персонал и руководство предлагают свои идеи для улучшения производства. Для каждого предложения рассчитываются показатели эффективности, которые помогают оценить успех инициативы.
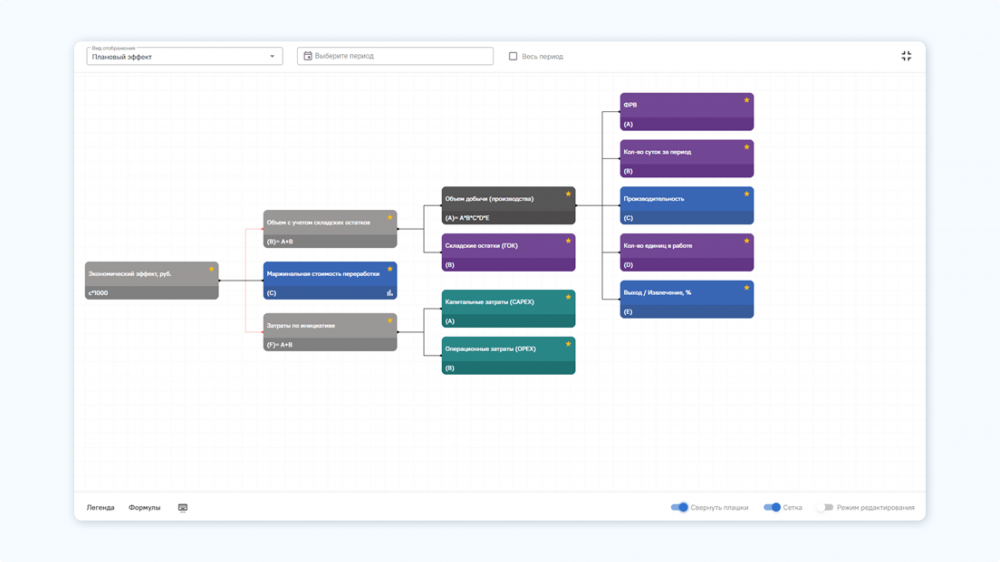
В системе есть планировщик задач, который помогает разбить внедрение на этапы, назначить ответственных и контролировать прогрессы. Так сотрудник всегда вовлечен в процесс и на основе каждого шага он может дополнять идею или предлагать новые.
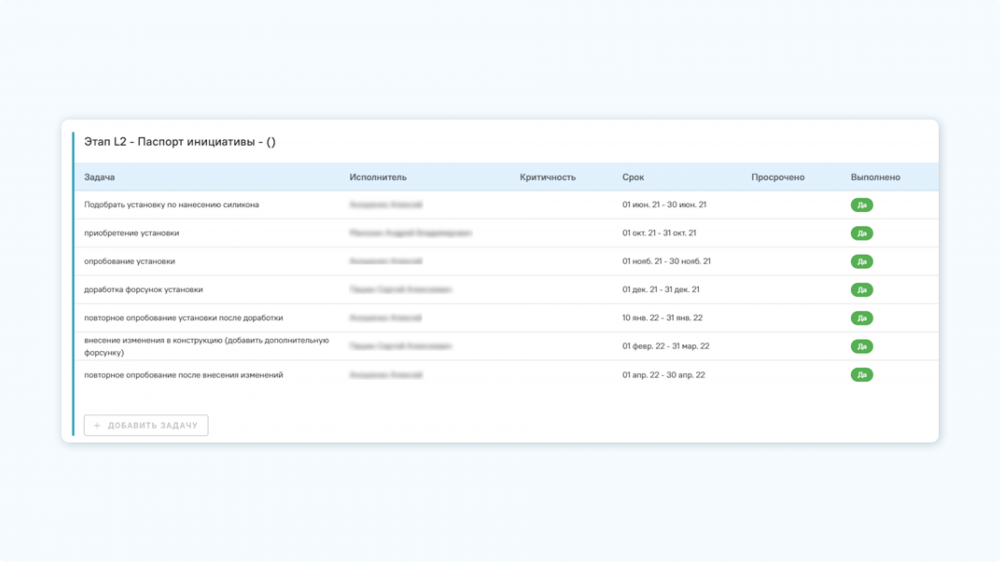
Чтобы наблюдать за всеми идеями и их реализацией — мы добавили отчеты и дашборды, которые пользователь может настроить под свои задачи.
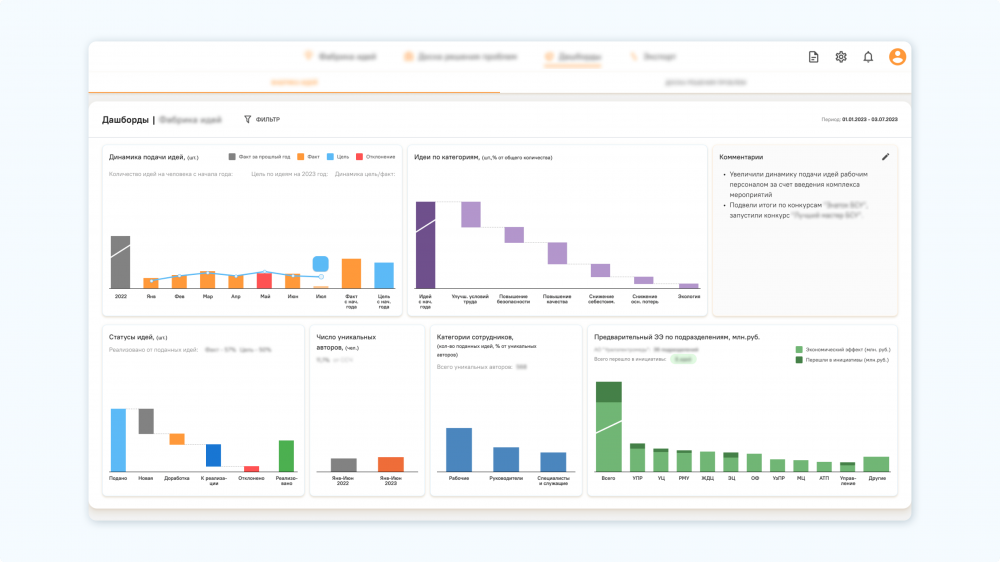
Наш продукт помог компании автоматизировать процесс проверки идей и привлечь более 1500 сотрудников из 34 компаний холдинга. Согласно промежуточным результатам, экономических эффект от идей, предложенных в системе, составляет 70 млрд рублей.
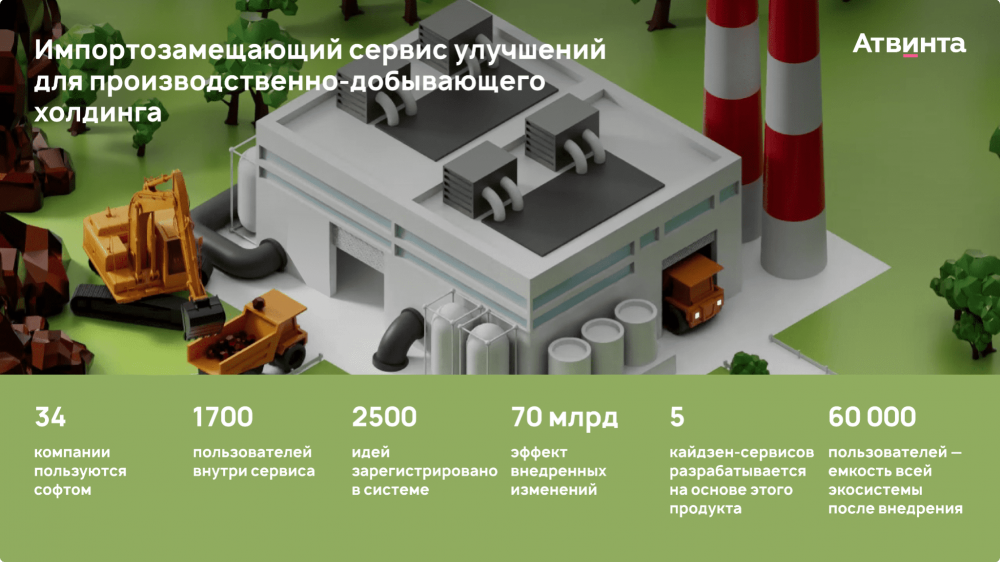
Инструменты бережливого производства
Чтобы минимизировать потери, используют инструменты lean production (существует более 25 видов). Условно их делят на методы планирования, анализа, контроля и управления качеством и регулирования конкретных процессов.
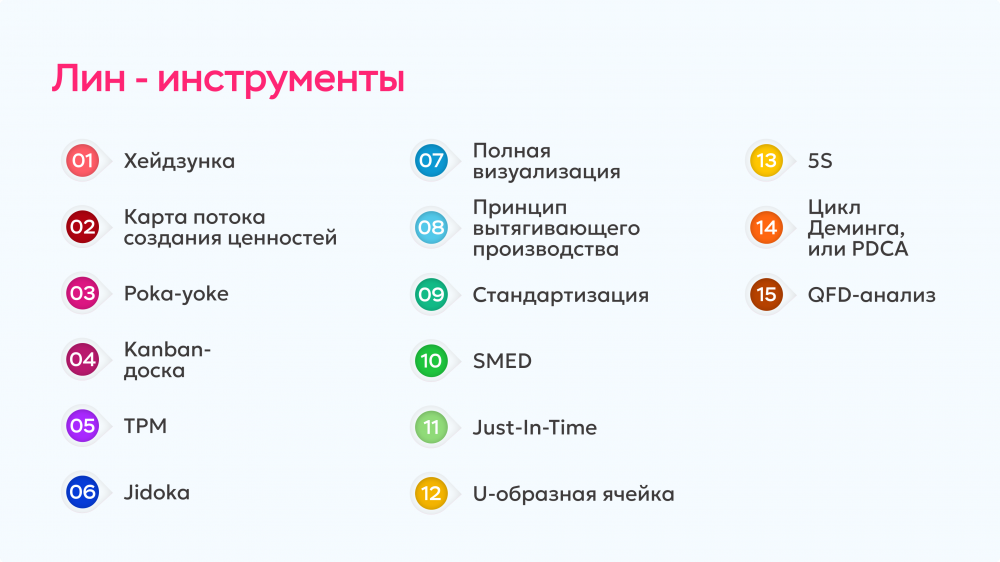
Карта потока создания ценностей
Систематизация потока ценности, или Value Stream Mapping (VSM) — способ визуализации текущего состояния производства и поиск ошибок, которые нужно устранить.
VSM представляет собой блок-схему, которая помогает планировать и внедрять нововведения. Например, чтобы сократить время сборки мебели за счет организации процесса доставки.
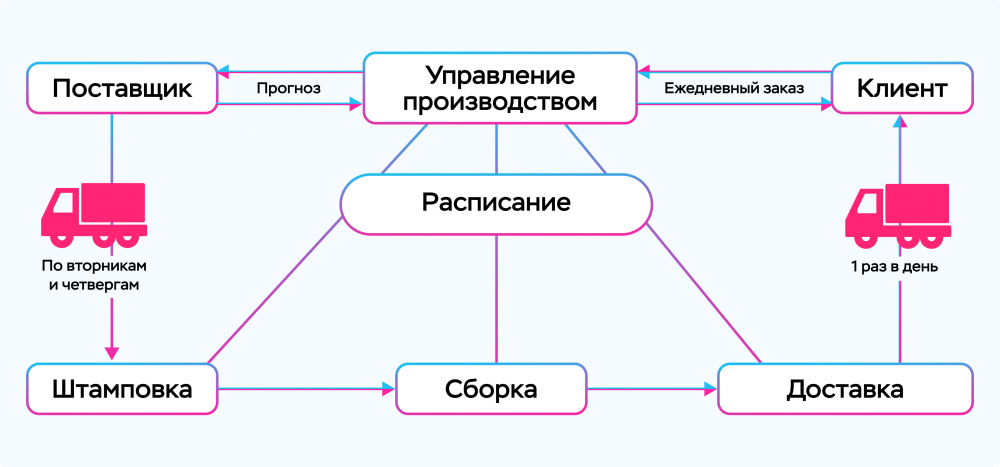
Методология канбан
Канбан-доска — система визуального управления процессами, которая показывает текущее состояние задач. Инструмент помогает распределить нагрузку и увидеть, сколько времени занимает отдельный этап работы.
Например, для металлургического холдинга, о котором мы рассказывали выше, наша команда сделала канбан для отслеживания статусов каждого предложения: от принятия идеи до ее реализации и расчета эффективности на каждом шаге.
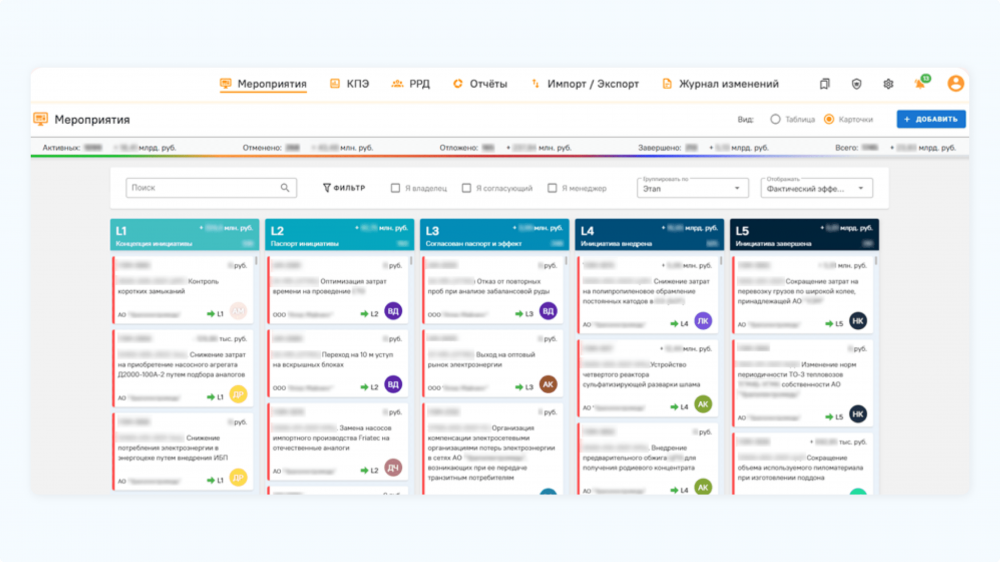
Полная визуализация
Подход показывает прозрачность производственных процессов — и сотрудники лучше разбираются в задачах и устройстве компании. Для реализации метода используют графики, диаграммы и блок-схемы. Они отображают каждый этап работы организации и данные по результатам: откуда приходят материалы, как осуществляется их обработка и какой получают продукт.
Цикл Деминга
Метод «Plan-Do-Check-Act» — способ для непрерывного улучшения продукта и производства с помощью четырех шагов: планирование, внедрение, проверка и коррекция новых правил. PDCA поможет увидеть проблему, внедрить гипотезу по ее устранению и изучить эффективность идеи. А затем дополнить предложение и запустить процесс заново.
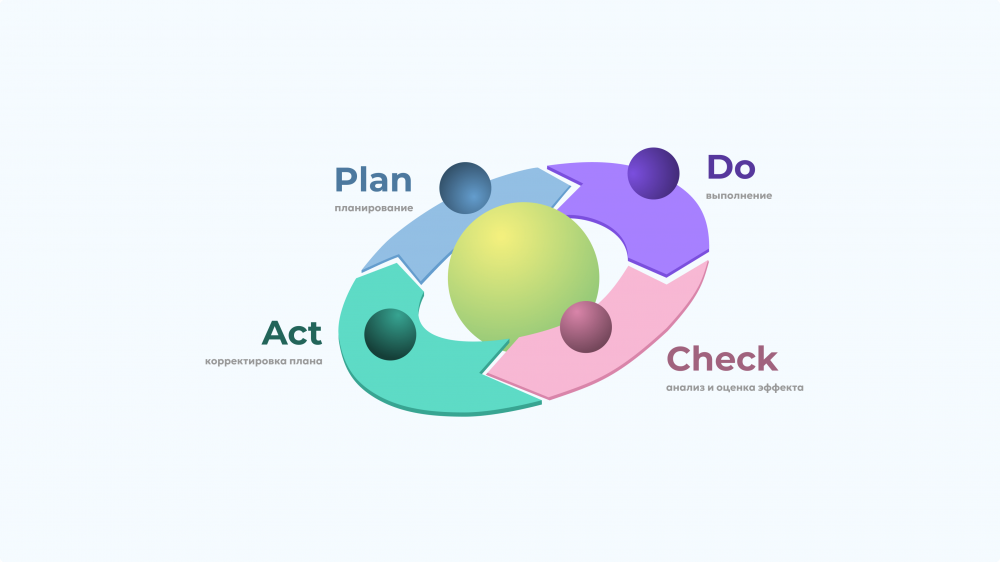
Стандартизация
Создание единых стандартов работы для повышения качества товара и продуктивности сотрудников. Документация выполнена в виде схемы, чтобы любой специалист мог разобраться в особенностях конкретной задачи.
Выравнивание спроса
Хейдзунка, или Heijunka — метод для стабилизации производственного процесса с помощью равномерного распределения нагрузки.
Нужно заранее собрать информацию по заказам, а затем производить одинаковое количество ассортимента каждый день. Это помогает избежать колебаний спроса и перегрузки оборудования, а также установить для сотрудников единый график работы.
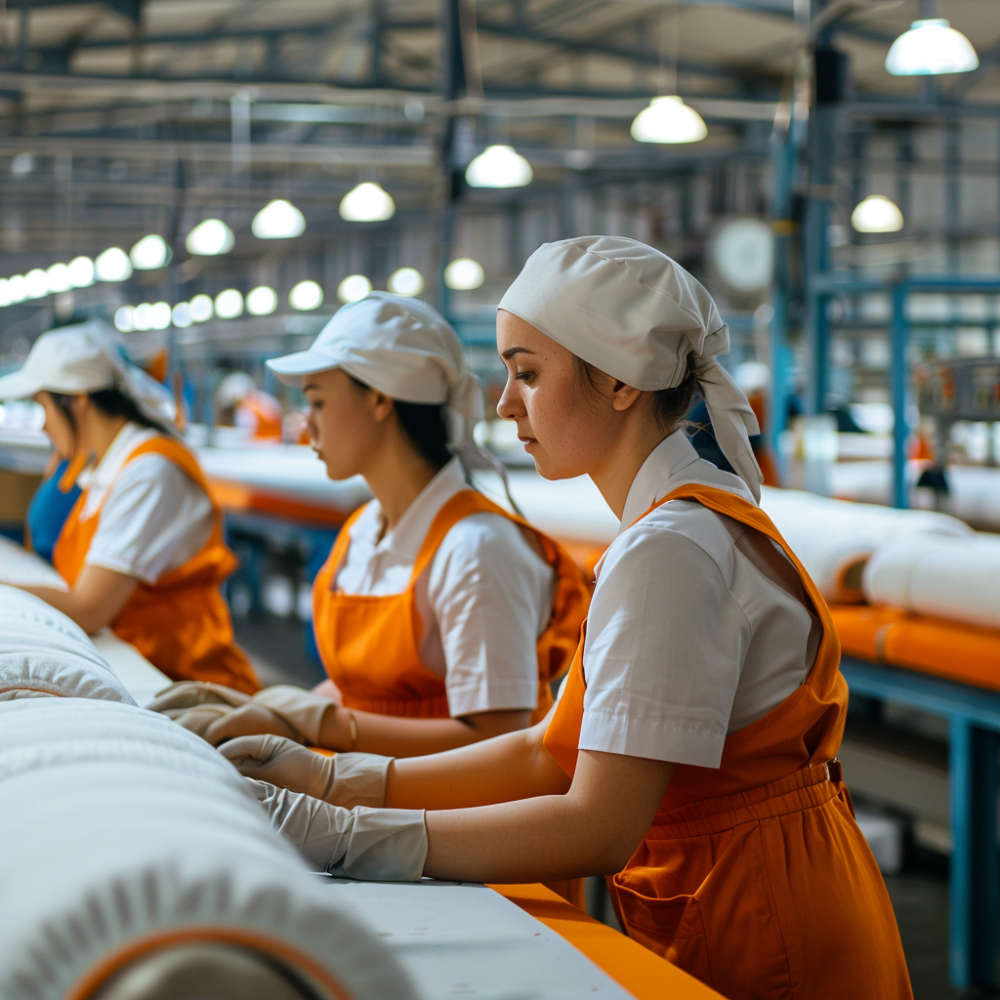
Защита от ошибки
Ноль дефектов, или Poka-yoke, Zero Defects (ZD) — способ предотвращения ошибок, вызванных человеческим фактором. Улучшения внедряют с помощью автоматизации ПО и регламентов. Например, разработка специальных датчиков, которые сигнализируют о неправильном положении детали. Такие решения уменьшают вероятность дефектов, повышают качество товаров и снижают издержки.
К примеру, можно внедрить ERP. Для предприятия «БЭКС», производящего комбикорм, мы разработали систему для контроля выпуска продукции и остатков, планирования загрузки производства и ведения продаж.
Одна из ключевых функций — автоматический расчет ингредиентов. Ранее технолог вручную указывал необходимый объем компонентов для замеса комбикорма. Если была допущена ошибка, вся партия считалась бракованной. Программа дала возможность минимизировать потери и ускорить процессы.
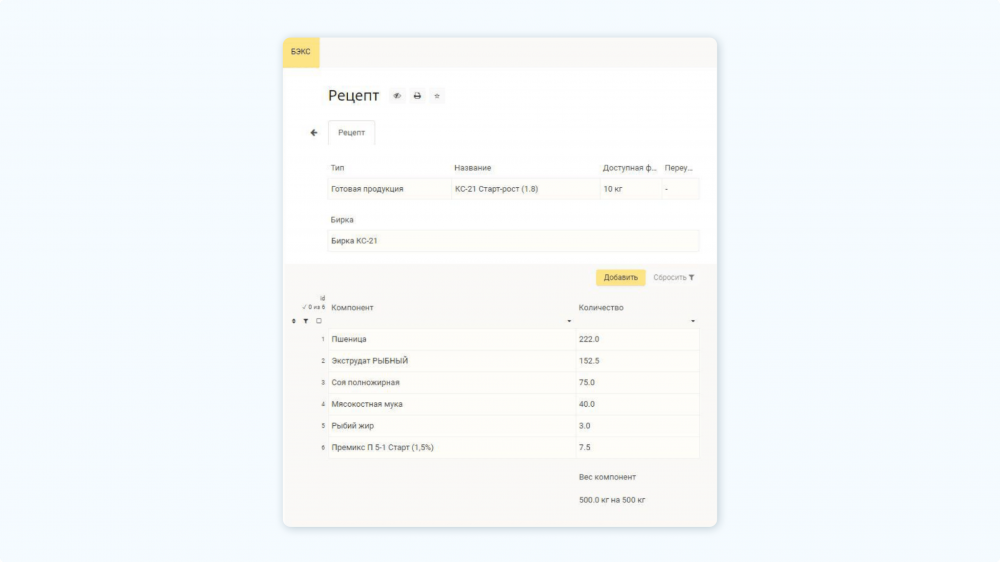
Всеобщий уход за оборудованием
Total Productive Maintenance (TPM) — подход, который помогает увеличить срок службы технического оснащения и уменьшить количество поломок, брака, задержек на производстве и несчастных случаев.
Сотрудники должны знать, когда нужно проводить уборку и плановое обслуживание. А также — к какому специалисту обращаться, если ПО выдает ошибку или инструмент плохо работает.
Дзидока
Автоматический контроль за качеством, который предотвращает выпуск дефектной продукции. Система предупреждает о возможной неисправности и тем самым помогает избежать перепроизводства и крупных расходов.
Принцип вытягивающего производства
Способ, который исключает перепроизводство и помогает создать продукт, отвечающий запросу клиента. Это нужно, чтобы задать сроки и объемы изготовления товаров, а также настроить гибкие процессы в компании. Так бренд может подстроиться под изменения рынка и оставаться конкурентоспособным.
Метод SMED
Single-Minute Exchange of Die, или быстрая переналадка — подход для быстрой настройки оборудования под другую задачу. Основная задача метода — сокращение простоев. То есть времени, когда технику нужно отключить, чтобы изменить параметры для следующего запуска.
Инструмент SMED помогает увидеть проблемы в организации процессов, а также в программном обеспечении (такие, как устаревшая версия сервиса).

Система Just-In-Time
Точно в срок, или JIT — управление ресурсами на производстве: материалы заказывают если они необходимы. Подход сокращает незавершенное производство и экономит пространство на складе.
U-образная ячейка
Метод организации рабочего места в виде буквы «U». Он нужен, чтобы сократить время сборки деталей и улучшить взаимодействие между сотрудниками.
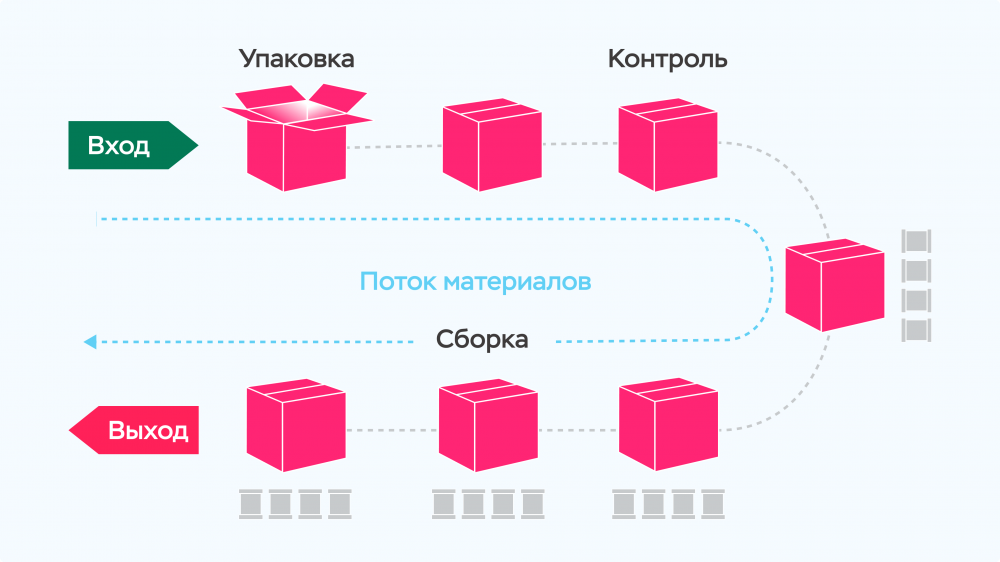
Метод 5S
Еще одна система для организации пространства, которая включает пять шагов:
- Сортировка — избавление от лишних предметов и мусора.
- Систематизация — размещение инструментов по своим местам. Например, материалы нужно вернуть на склад на ту же полку, с которой ее взяли.
- Соблюдение чистоты — наведение порядка в процессах, задачах и даже рабочих чатах, чтобы не потерять важную информацию.
- Стандартизация — разработка правил, которые помогут автоматизировать работу и всегда придерживаться первых трех пунктов.
- Совершенствование — непрерывное улучшение системы для повышения эффективности и создания оптимальных условий труда.
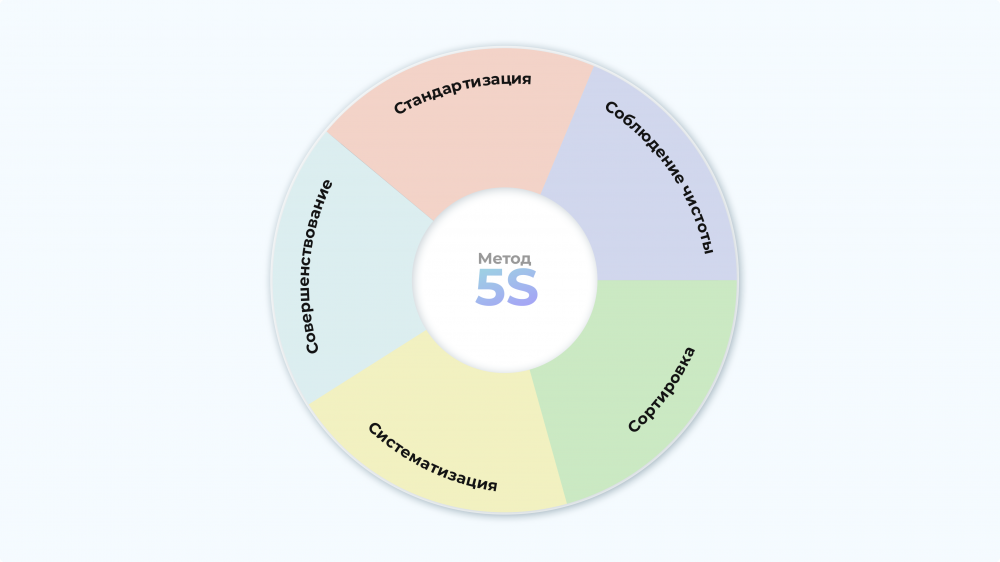
QFD-анализ
Суть метода: чем лучше продукт соответствует требованиям и ожиданиям клиента, тем успешнее он будет на рынке. QFD-анализ позволяет систематизировать пожелания и перевести их в конкретные характеристики товара или услуги.
Рассмотрим пример нашего партнера и клиента GoodLine, который уже несколько лет активно внедряет стандарты бережливого производства во все бизнес-процессы. В 2022 году компания начала вносить улучшения на свой склад: сначала физическую часть, а затем и автоматическую. Изменения нужны были, чтобы минимизировать количество брака, исключить лишние действия в процессе сборки заказов, а также корректно вести учет товаров и иметь к ним быстрый доступ.
Физическая часть — это улучшение рабочего пространства на складе. Всю продукцию пересчитали, поделили на категории, разложили по ячейкам и подписали: наименования и штрихкоды. Выбросили мусор, а лишние детали и ненужное оборудование отдали или продали. Это помогло расчистить четыре помещения площадью 1600 кв. м., создать вертикальное хранение на 420 кв. м. и разметить рабочие зоны: отгрузка, сервис и хранение. На первом этапе удалось сократить потери и значительно увеличить эффективность.
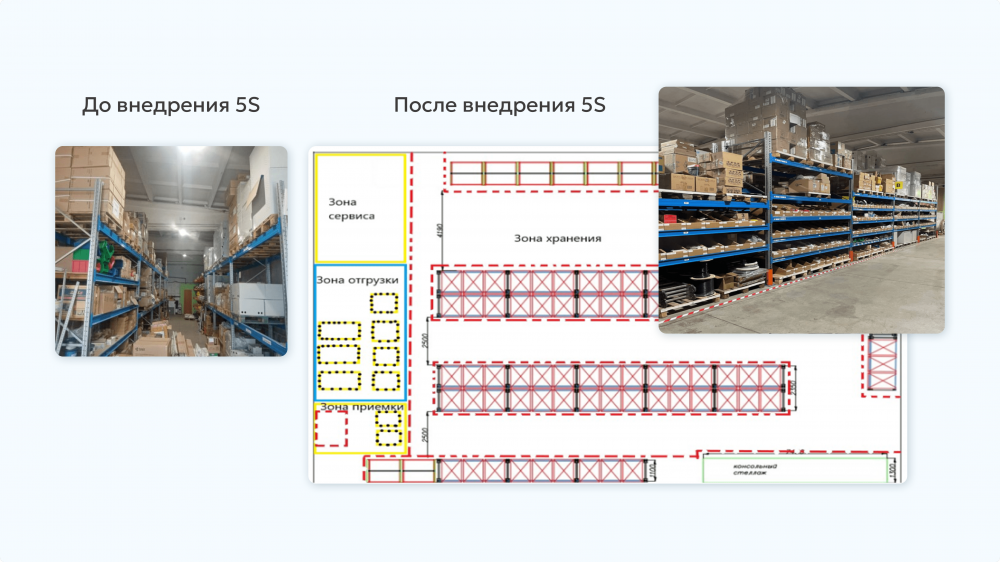
Чтобы правильно внедрить улучшения, использовали более десяти лин-инструментов. Сначала изучили каждый процесс, нашли и обозначали проблемы и первопричины с помощью диаграммы Исикавы. А затем начали предлагать решения и создавать регламенты.
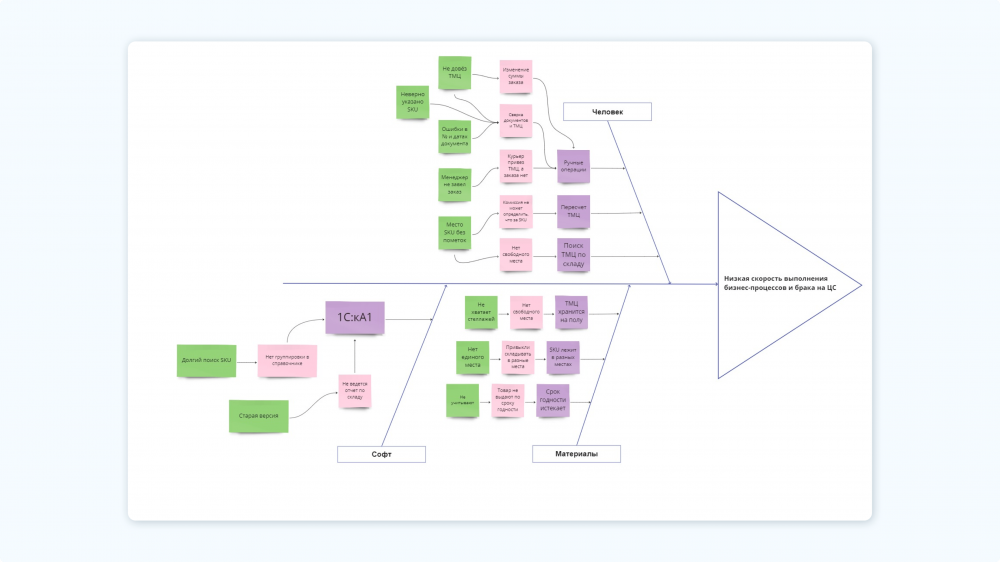
Автоматическая часть — разработка сервиса, который упрощает сборку заказов, минимизирует брак и пересорт, помогает проводить инвентаризацию с точностью до 99,97% и контролировать остатки. Программа улучшила общение между отделами, которым ранее приходилось звонить или идти на склад, чтобы дать задачу. Также сократилось время обучения сотрудников — например, раньше кладовщику на подготовку требовалось полтора месяца, сейчас же это занимает 10 минут.
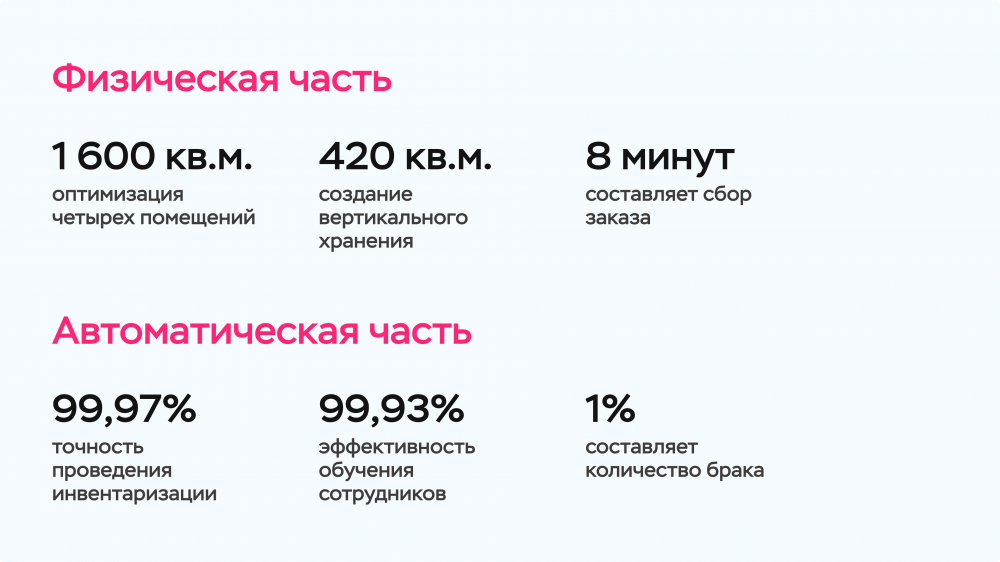
Подведем итоги
Система бережливого производства направлена на оптимизацию производственных процессов и улучшение эффективности компании. Применение инструментов позволяет сократить потери и повысить качество продукции.
Однако, несмотря на плюсы, во время внедрения можно столкнуться со сложностями. Например, саботаж изменений в корпоративной культуре или недостаточное бюджетирование для новой системы менеджмента.
Ключевым аспектом lean production является системный подход к управлению. Это не только техническое оснащение, но и развитие кадрового потенциала и постоянное стремление к улучшению. Сочетание принципов, методов и инструментов бережливого производства позволяет компаниям добиваться успеха и сохранять конкурентоспособность в долгосрочной перспективе.
Мы в Атвинте помогаем компаниям оцифровать лин с помощью разработки специализированного ПО. Это может быть онлайн-пространство для сбора и хранения идей сотрудников или масштабный сервис с полноценным циклом: от фиксации инициатив до их внедрения и расчет экономического эффекта.
0
0
0
Услуги
Читайте также
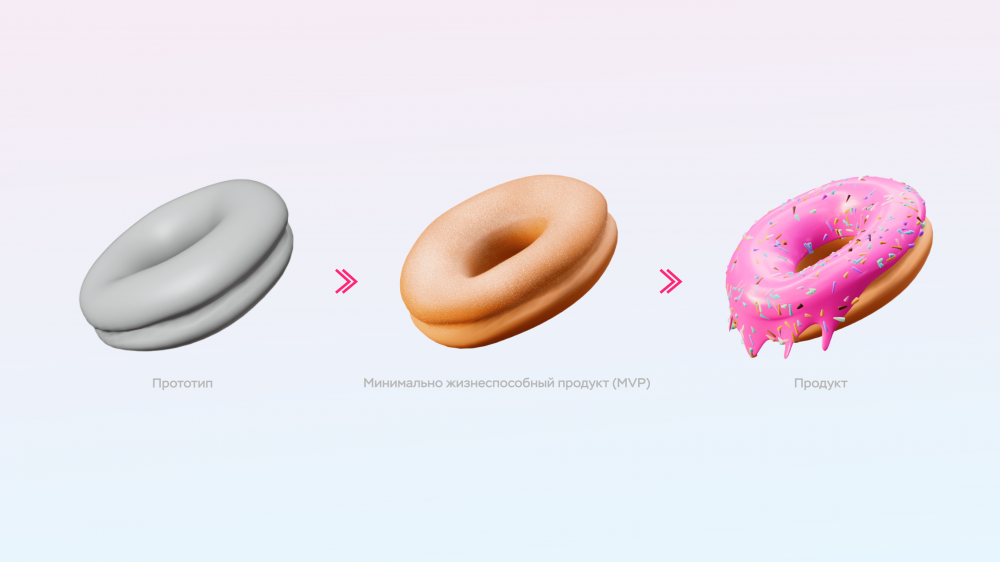
MVP продукта: зачем и когда использовать
Раскрываем особенности разработки MVP, его виды и преимущества, а также как минимально жизнеспособный продукт может помочь вашему бизнесу.
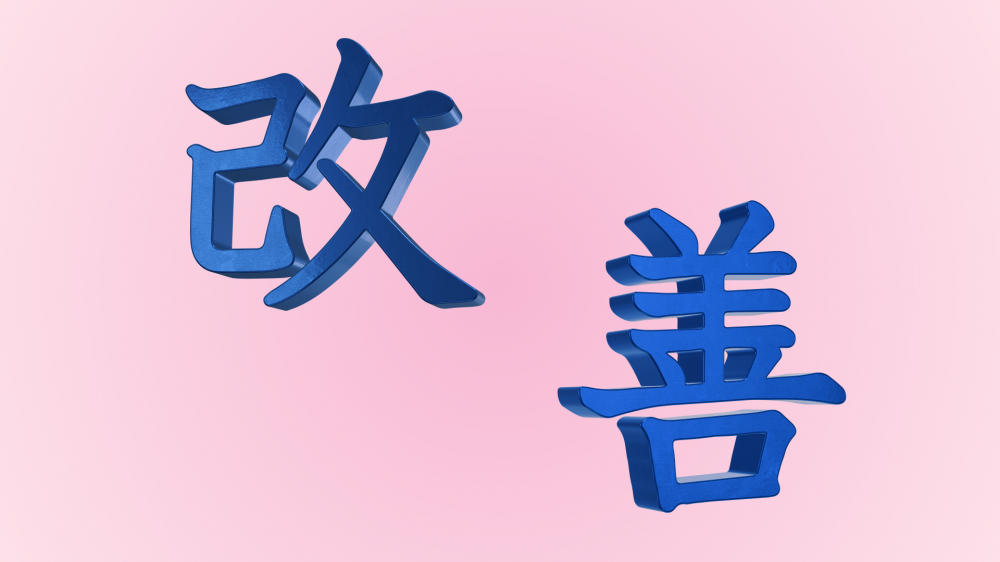
Непрерывное развитие по системе кайдзен: основы и методы
Рассказываем, как применять принципы и методы системы управления кайдзен и как эта философия влияет на процессы и качество продукта.