Производительность труда без потерь: как увеличить показатели с помощью бережливого производства
Бизнес и эффективность
ИТ в промышленности
24 апреля 2025
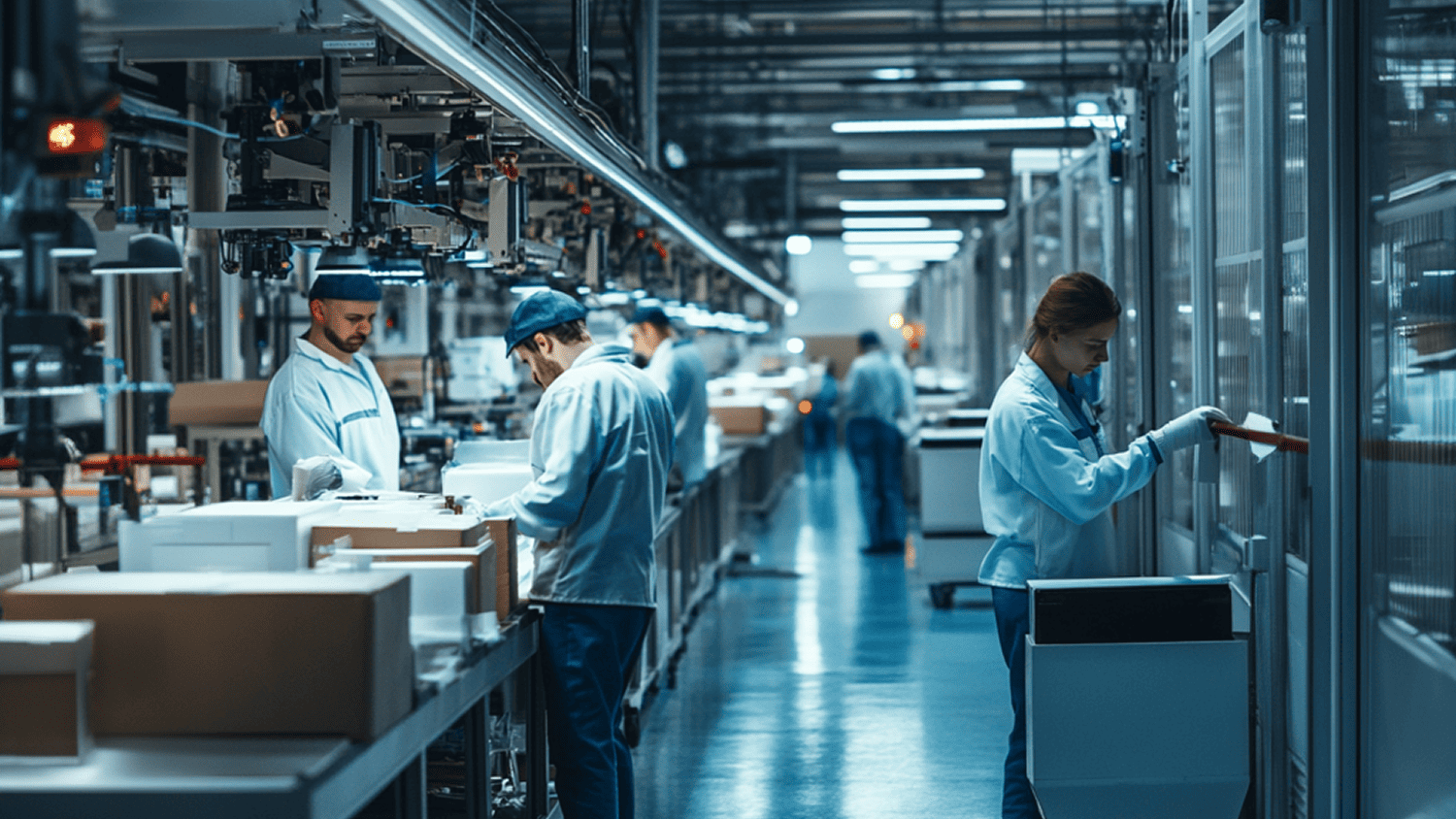
Производительность труда — это про то, как устроены процессы, где теряется время и внимание сотрудников, и насколько компания умеет превращать идеи в улучшения.
На многих предприятиях предложения по оптимизации возникают стихийно: кто-то что-то заметил, написал в чат, передал устно или занес в таблицу. Но без единого подхода и понятной системы такие инициативы быстро тонут в рутине. Процессы продолжают буксовать, а производительность — стоять на месте.
Концепция бережливого производства (lean) помогает выстроить структуру: где находить потери, на что смотреть в первую очередь и как вовлекать сотрудников. Чтобы методика действительно работала, ей нужен цифровой инструмент, который делает улучшения управляемыми и измеримыми.
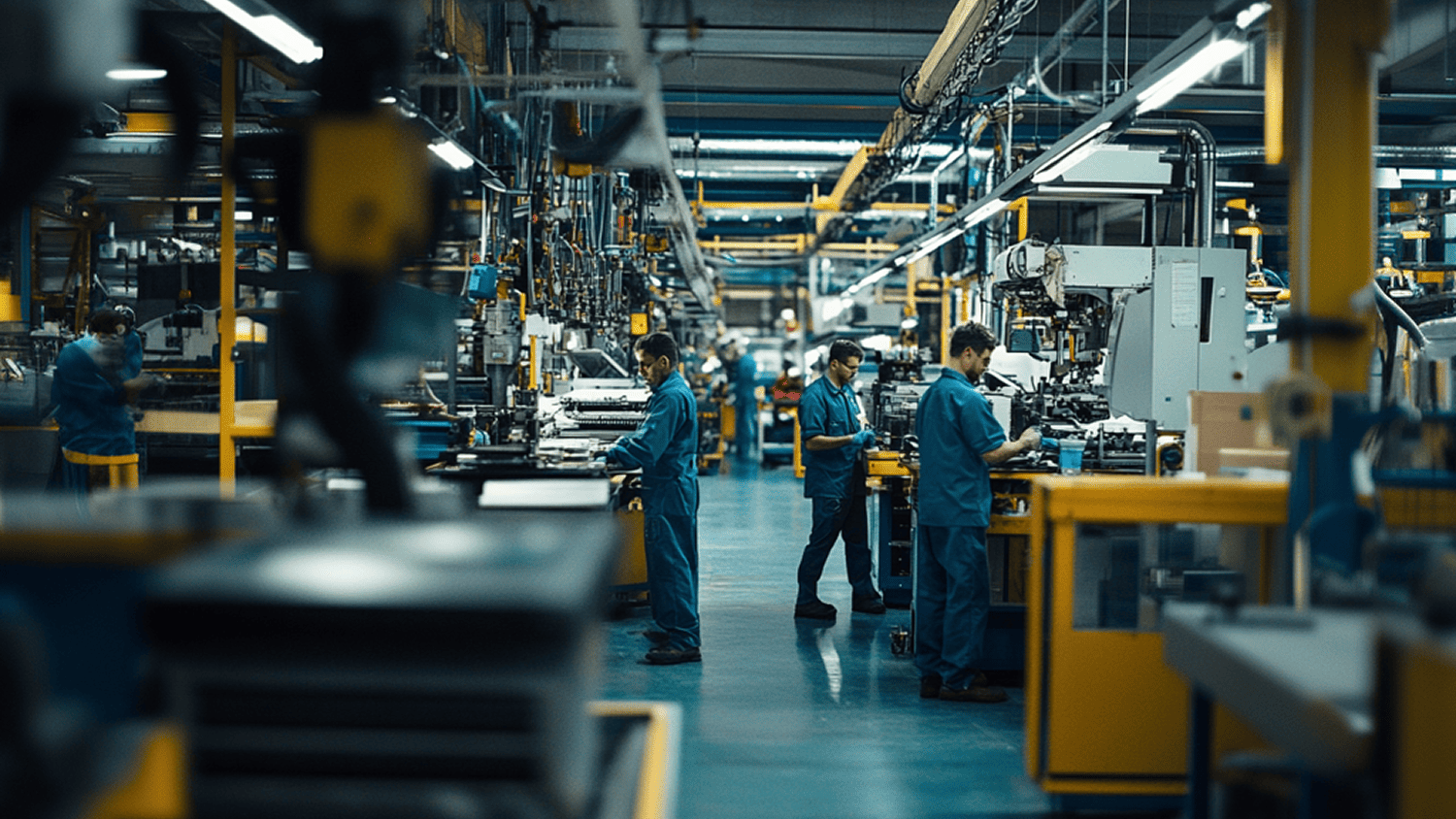
Технологии помогают систематизировать предложения, убрать лишнюю ручную работу и ускорить принятие решений. А главное — превратить разрозненные идеи в понятный поток, который можно внедрять, отслеживать и масштабировать.
В этой статье расскажем, как бережливое производство и цифровые инструменты повышают производительность труда.
Что тормозит производительность труда
На производстве можно увидеть парадоксальную картину: люди заняты, станки работают, отчеты сдаются — но результаты не растут. Причина заключается в скрытых барьерах, которые замедляют операции и мешают команде двигаться быстрее.
Потери в операционной деятельности
В лин-подходе выделяют восемь видов потерь, которые напрямую влияют на производительность. Они могут быть незаметны с первого взгляда, но именно эти проблемы ежедневно тормозят работу.
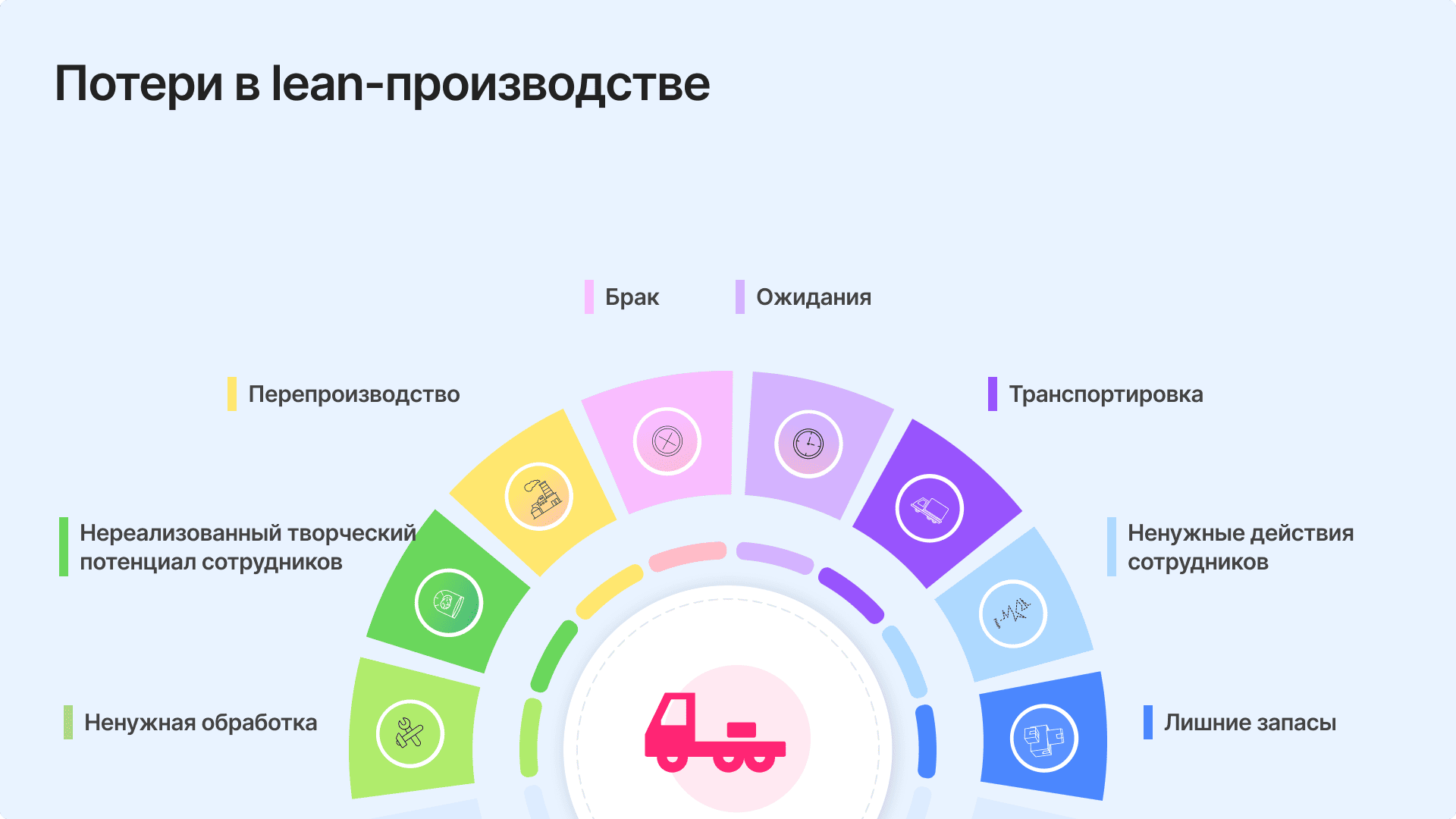
- Перепроизводство — это выпуск большого количества изделий, чем требуется на текущий момент. Например, участок изготавливает детали с опережением, но сборка не успевает их принять — в итоге заказы копятся, а время сотрудников тратится впустую.
- Ожидание — простой оборудования из-за задержек. К примеру, оператор не может начать работу, пока не придут результаты измерений или не доставят инструмент.
- Транспортировка — перемещения, которые не добавляют ценности продукту. Например, материалы везут из одного цеха в другой, хотя их можно было расположить ближе. Чем больше лишних перемещений — тем выше износ и риск задержек.
- Лишние запасы — это закупка или производство «на всякий случай». Склады забиваются сырьем, которое не используется — это замороженные деньги и логистическая перегрузка.
- Ненужные движения. Когда сотрудники выполняют действия, не приближающие их к результату. Например, поиск нужного инструмента по всему участку.
- Избыточная обработка — выполнение операций, не влияющих на качество продукта. Например, финишная обработка деталей включала повторную полировку, хотя по ТЗ это было избыточным действием, которое тратило время сотрудника.
- Брак — переделка или списание из-за ошибок. Неправильные параметры и сбой станка — все это требует времени и ресурсов на исправление.
- Нереализованные идеи сотрудников — предложения, которые могли бы устранить потери, но они не дошли до реализации.
Разрозненность процессов
Один отдел использует Excel, другой общается через мессенджеры, третий — оформляет заявки на бумаге. Даже простая инициатива по улучшению может затеряться между согласованиями. Когда каждый работает по своей схеме, управляемость исчезает. Все держится на личной инициативе, а не на системе.
Потери внимания и времени
Сотрудники тратят часы на поиск нужных документов, ожидание ответа от коллег, оформление форм и участие в неэффективных совещаниях. В условиях постоянной текучки и перегрузки это выматывает — мотивация падает, а вместе с ней исчезают и инициативы по улучшениям.
Ручное управление
Без автоматизации процессы завязаны на людях: кто должен напомнить, передать информацию и проследить за выполнением. Чем больше участников — тем выше риск задержек и сбоев.
Как бережливое производство повышает производительность труда
Бережливое производство помогает сосредоточиться на главном: убрать лишнее, выровнять процессы и дать людям возможность работать без постоянных сбоев.
Снижение избыточных операций
В каждом производственном процессе есть действия, которые не добавляют ценности. Перепроверки, дублирующие отчеты, повторная передача информации между отделами — все это съедает время и силы. Lean-инструменты помогают выявить узкие места и убрать «фантомную» занятость. В итоге сотрудник делает меньше лишних действий и больше полезных.
Выравнивание процессов и устранение простоев
Когда в компании выстроена логика процессов и понятны роли участников — снижаются задержки и простои. Действия становятся предсказуемым: не нужно ждать согласований, уточнять приоритеты или разбираться, кто за что отвечает.
Вовлечение сотрудников в улучшения
Сотрудник, который каждый день работает в конкретном процессе, первым замечает проблемы и узкие места. Если у него есть простой и понятный инструмент для подачи предложений — он включается в развитие рабочего пространства и компании в целом.
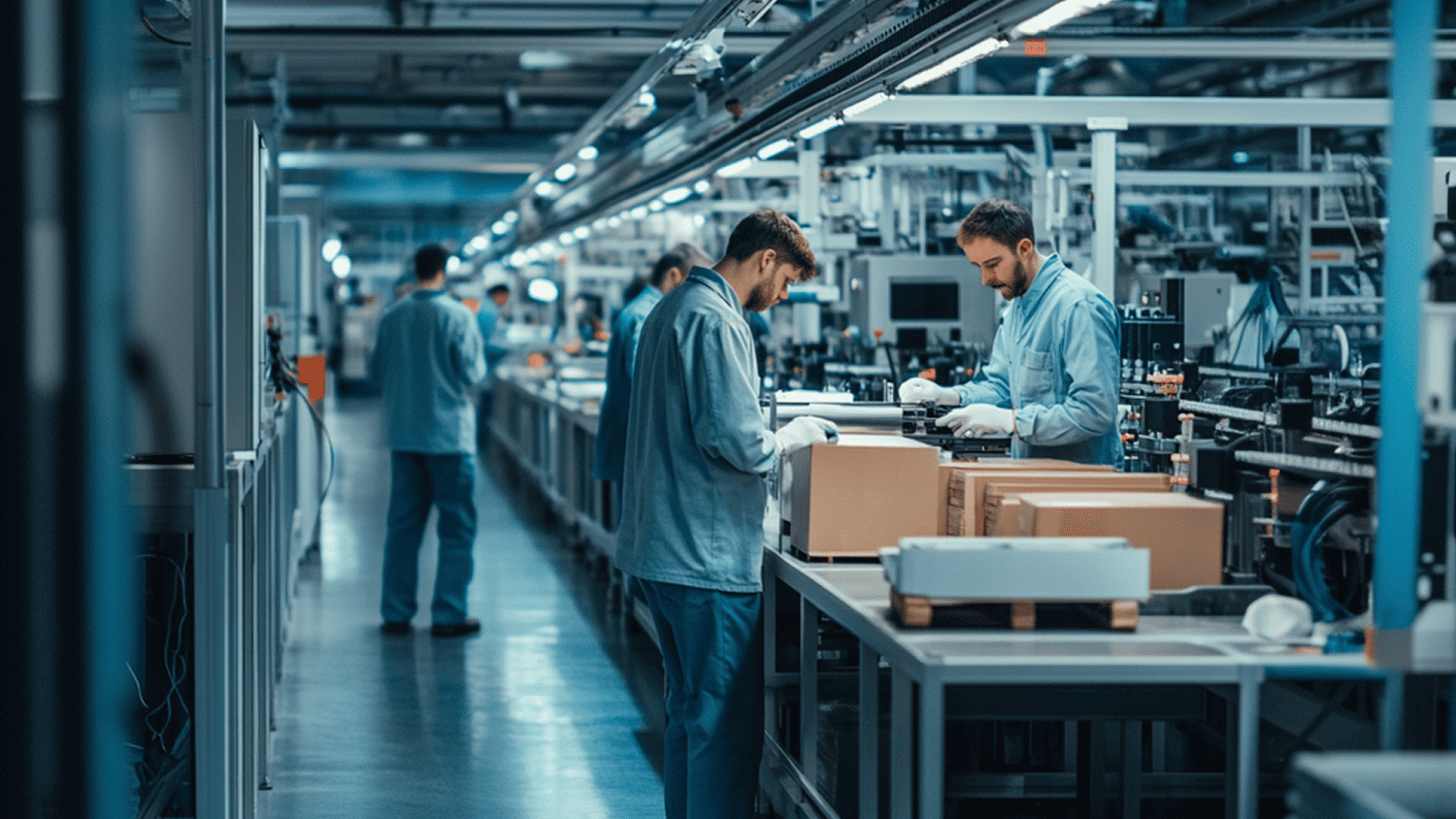
Как технологии влияют на бережливое производство
Бережливое производство строится на постоянных улучшениях и устранении потерь. Когда компания растет, управлять изменениями вручную становится невозможно. Чем больше данных, задач и участников — тем выше нагрузка на процессы. Цифровизация дополняет лин-подход в реальных и быстро меняющихся условиях.
Цифровые продукты
Автоматизация берет на себя рутину: сбор предложений, маршрутизацию, уведомления и контроль сроков. То, что раньше решалось через десятки писем и совещаний, система делает за секунды. В результате у сотрудников освобождаются ресурсы, которые можно направить на сами улучшения.
Мы сотрудничаем с крупным промышленным холдингом, где до этого сбор идей по улучшениям вели на бумажных носителях. Это тормозило внедрение и увеличивало время на согласования. Наша команда создала единую цифровую экосистему для работы с инициативами: от подачи предложения до их реализации.
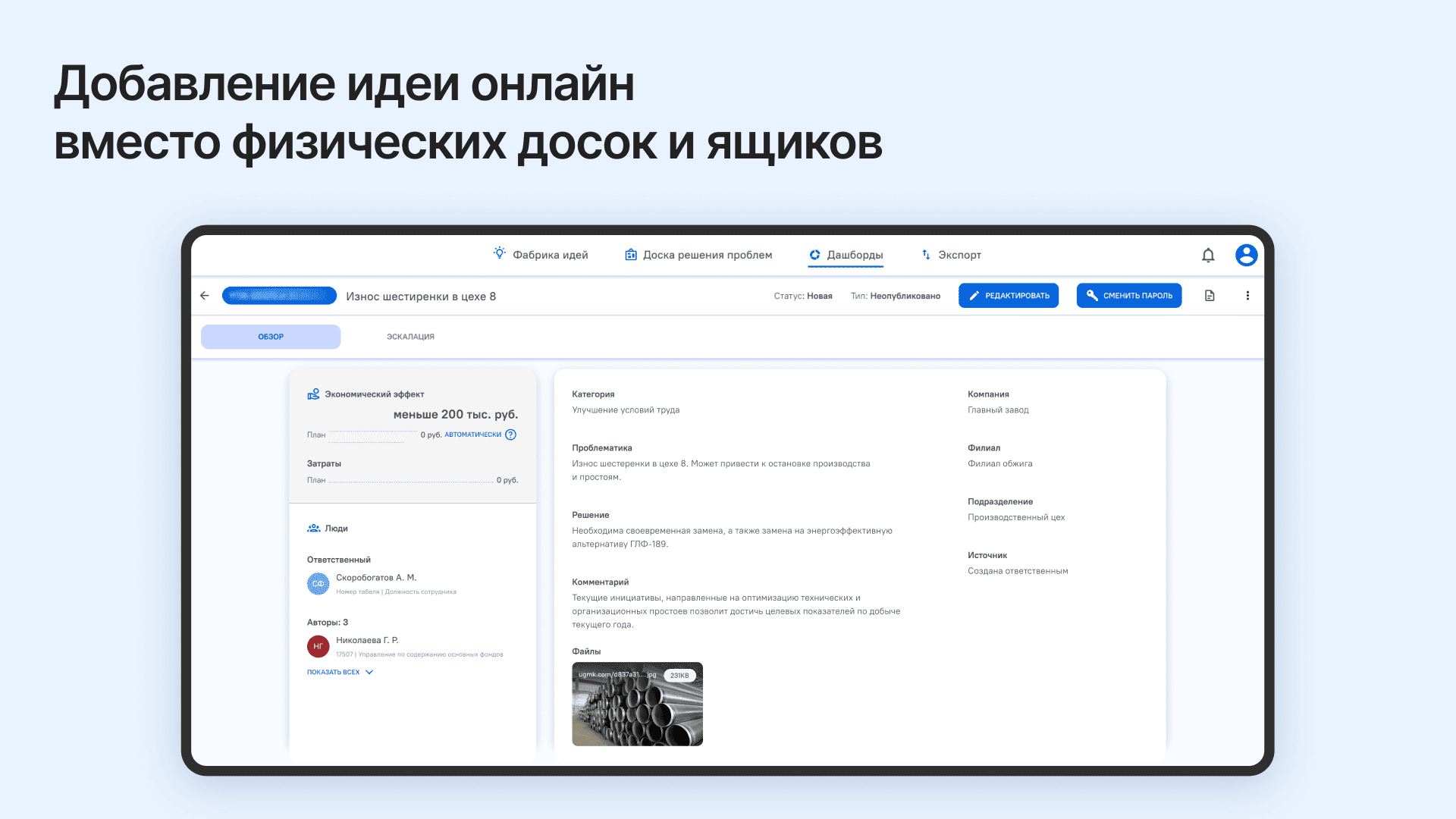
Запустили сервис трансформационных предложений — он обрабатывает инициативы с экономическим эффектом от 1 млн рублей. После этого появилась «Фабрика идей» для предложений меньшего масштаба — до 1 млн рублей. Обе системы интегрированы между собой: у них общий кабинет, простой интерфейс, визуализация статусов и трекинг реализации предложений.
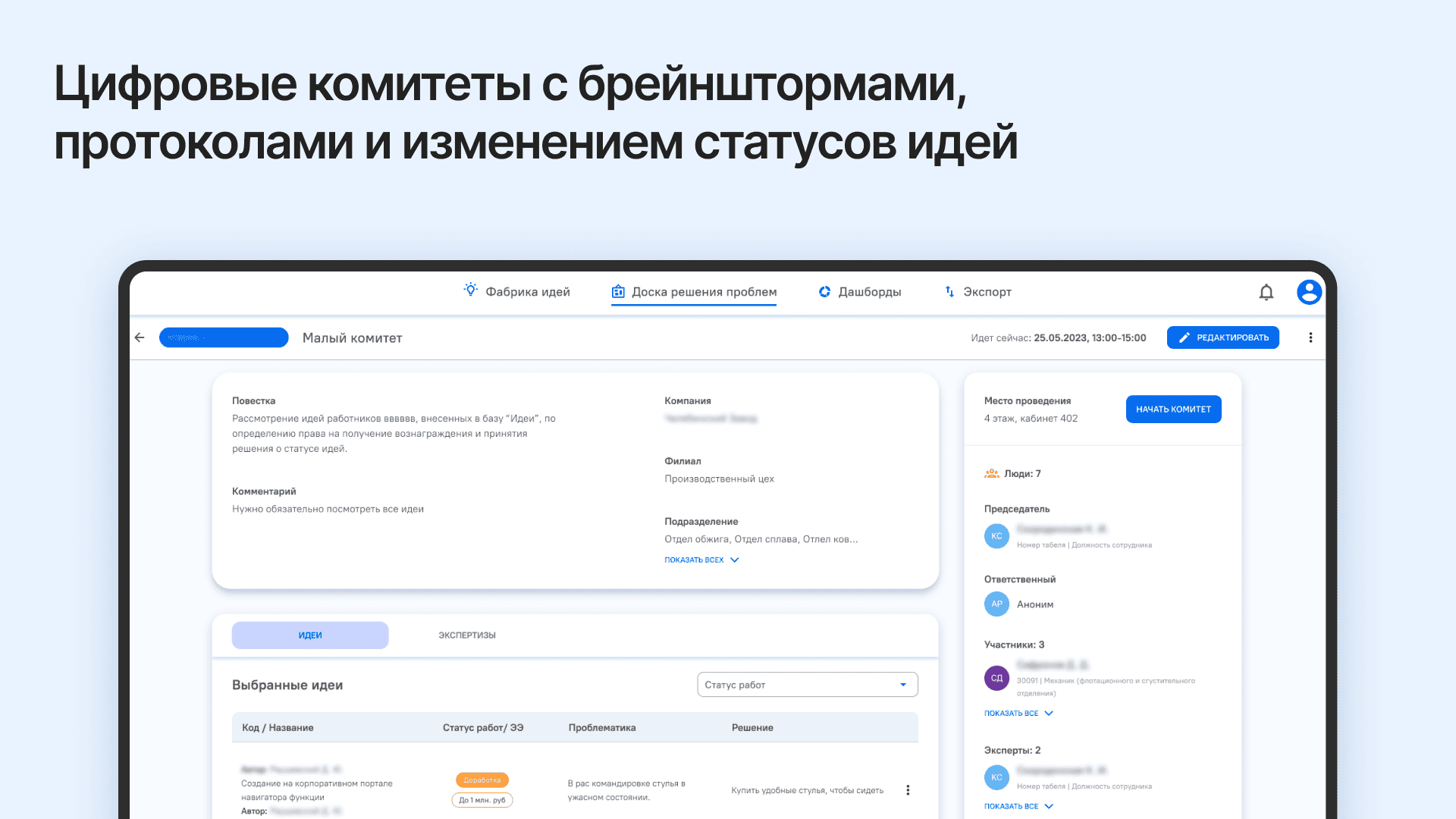
Цифровые инструменты создают прозрачность. Каждый участник процесса видит, на каком этапе находится задача, кто отвечает за следующий шаг, и какой эффект это дает. В системах визуализации и дашбордах нет места догадкам — все видно сразу: от загрузки команды до экономического результата.
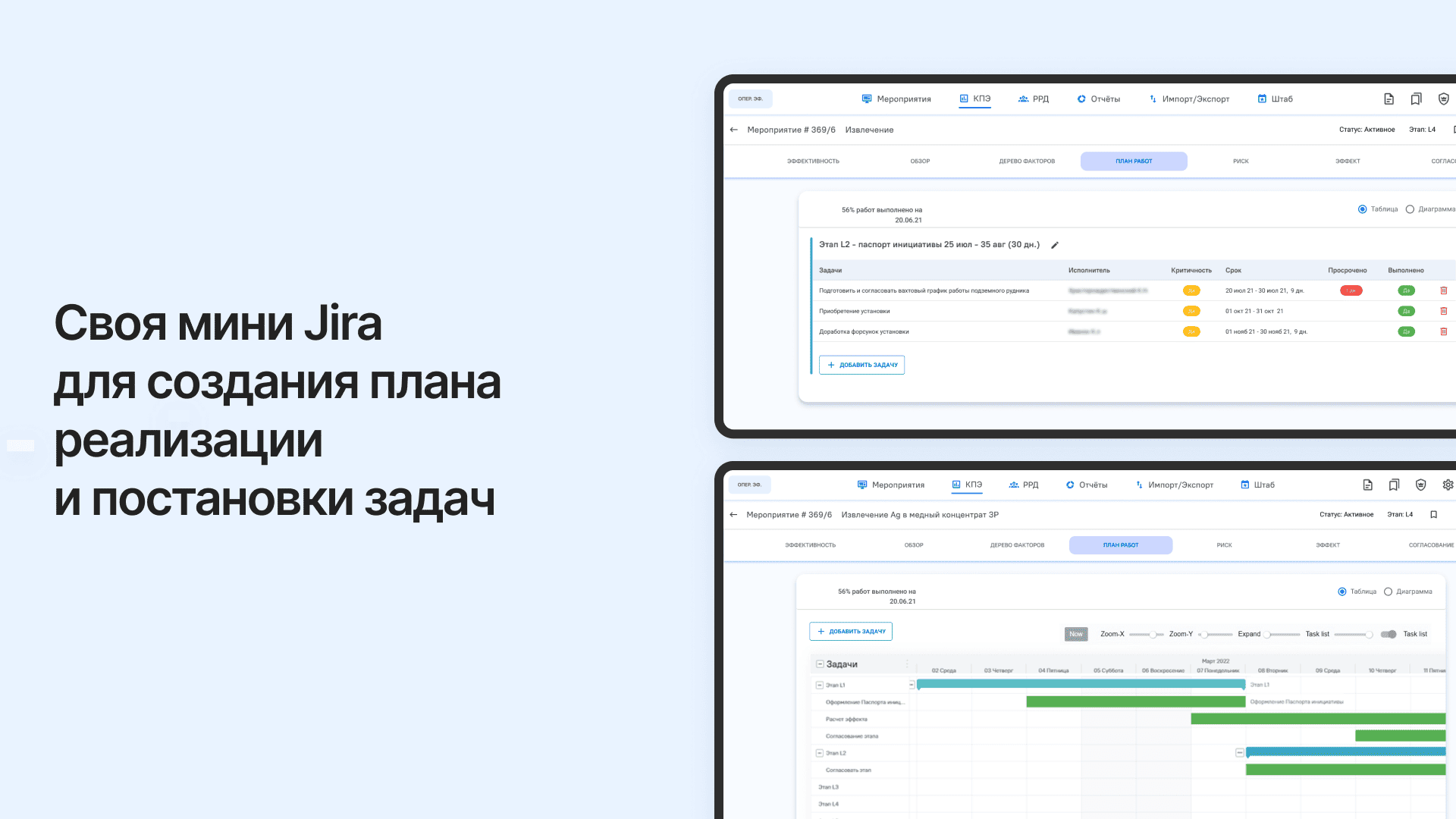
Получение обратной связи и избавление от хаоса
Одно из главных препятствий — молчание со стороны руководства и системы. Когда идея уходит «в никуда», человек второй раз ее не предложит. Цифровые инструменты помогают собрать обратную связь:
- сотрудник сразу видит статус предложения — «на рассмотрении», «в работе», «реализовано» или «отклонено»;
- все участники получают уведомления;
- обсуждения происходят в чате или во время созвона прямо в системе.
В итоге все процессы прозрачны и каждый участник знает, на каком этапе находится идея.
В разработанной нами экосистеме сотрудники подали более 50 000 предложений. Все инициативы проходят экспертизу, согласование и внедрение. В результате компания получила подтвержденный экономический эффект в 20 млрд рублей. Такие результаты возможны только тогда, когда улучшения становятся частью повседневной работы и корпоративной культуры на предприятии.
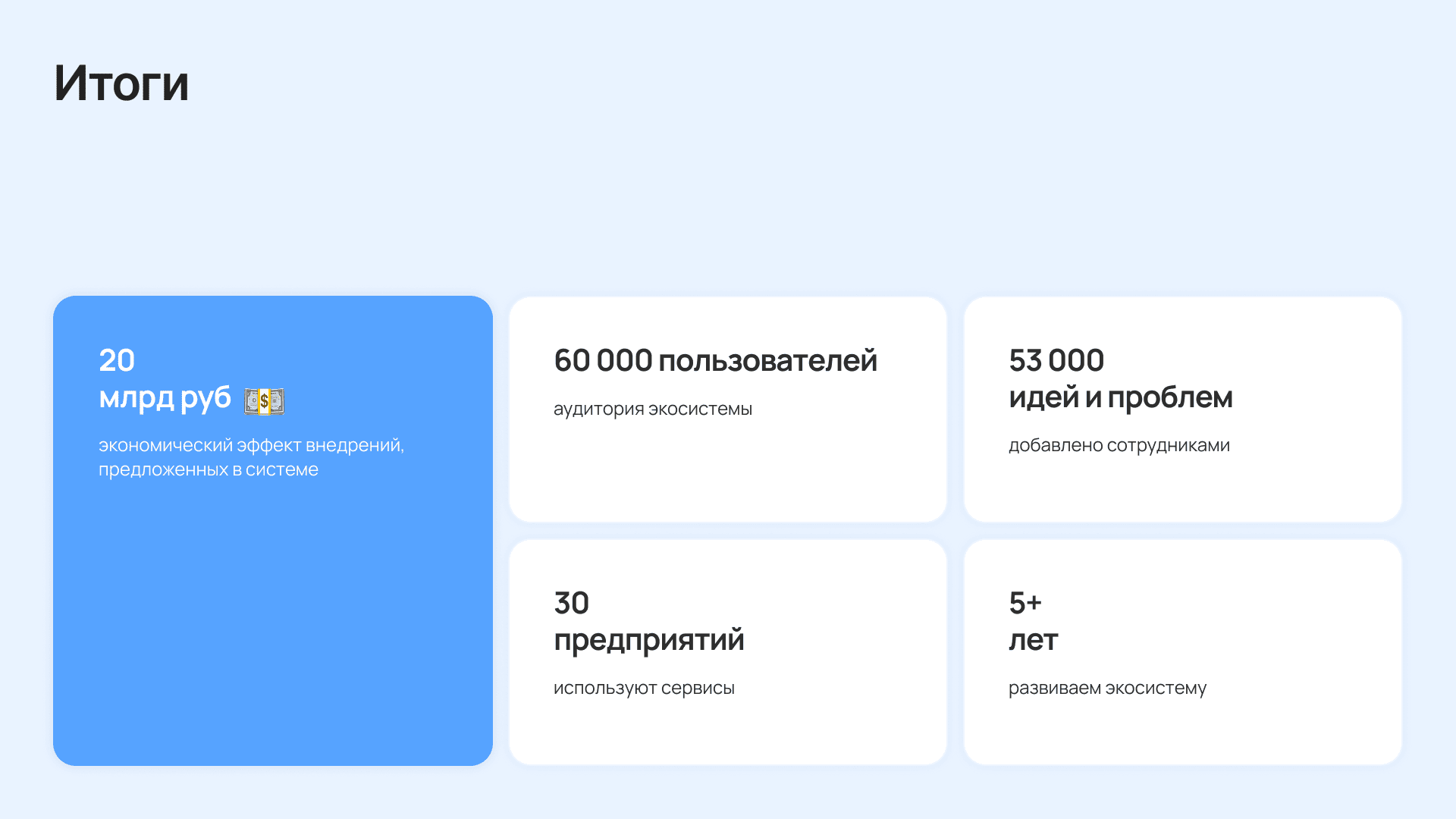
Быстрое включение новых сотрудников
Для нового сотрудника важно с первых дней понимать, как устроены процессы, куда можно подать идею и где найти нужную информацию. Если в компании внедрен цифровой инструмент с lean-логикой, система сама подсказывает следующие шаги — без необходимости спрашивать у коллег: «Что делать?».
В некоторых компаниях такую адаптацию усиливают с помощью экспертных сообществ — цифровых площадок, где сотрудники могут задавать вопросы, обмениваться опытом и получать консультации по конкретным задачам.
Развивая экосистему для холдинга, мы разработали подобную соцсеть, которая объединяет десятки тематических сообществ: от технологий и ремонта до охраны труда. В сервисе есть каталог экспертов, внутренняя база знаний, обучающие видео и тематические обсуждения.
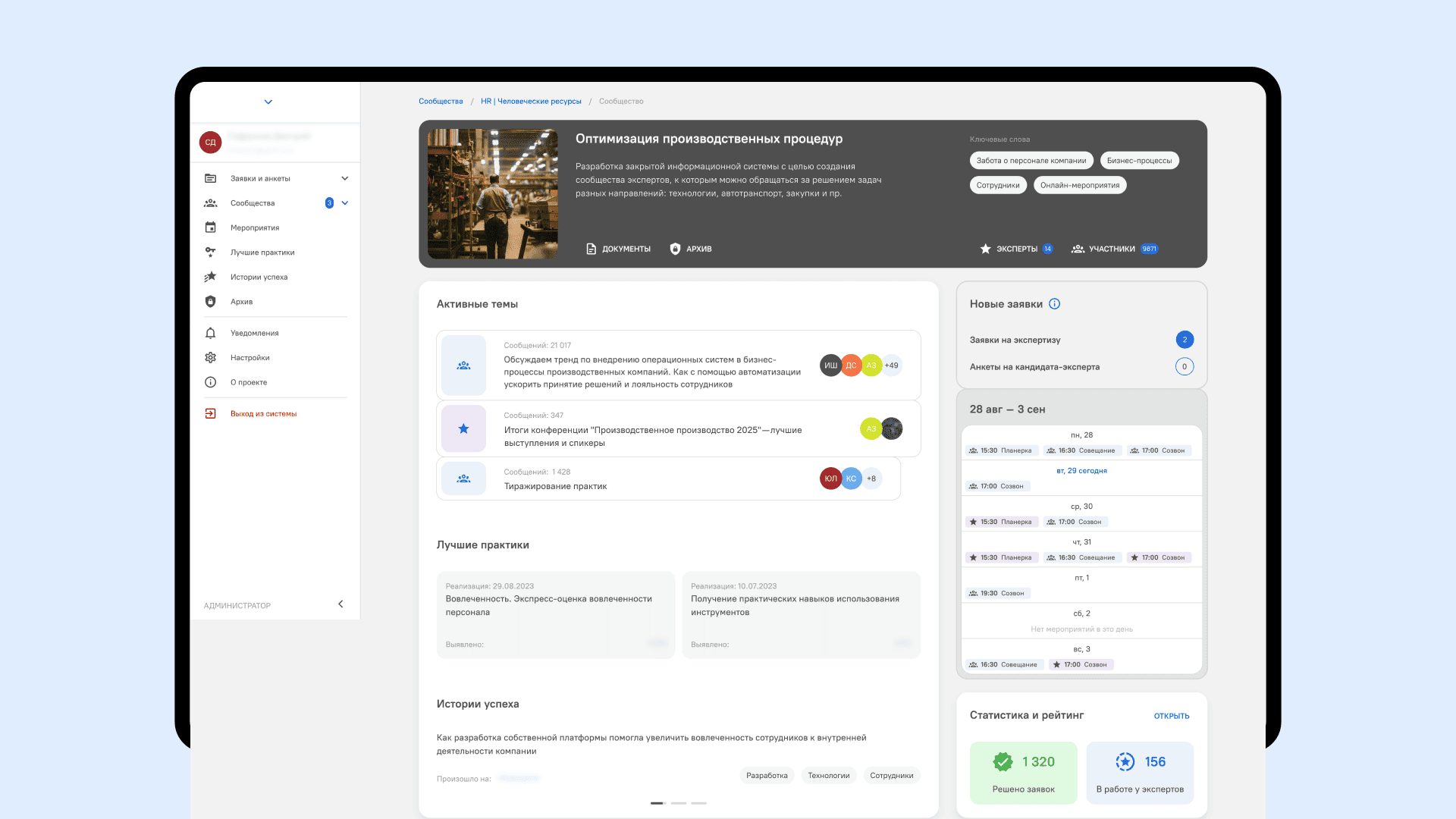
Для обучения и передачи опыта мы встроили:
- библиотеку лучших практик с реальными примерами внедрений и их результатами;
- видеоплатформу — безопасный корпоративный аналог Ютуба с инструкциями и демонстрациями;
- рейтинги и баллы, которые мотивируют экспертов помогать коллегам и делиться знаниями.
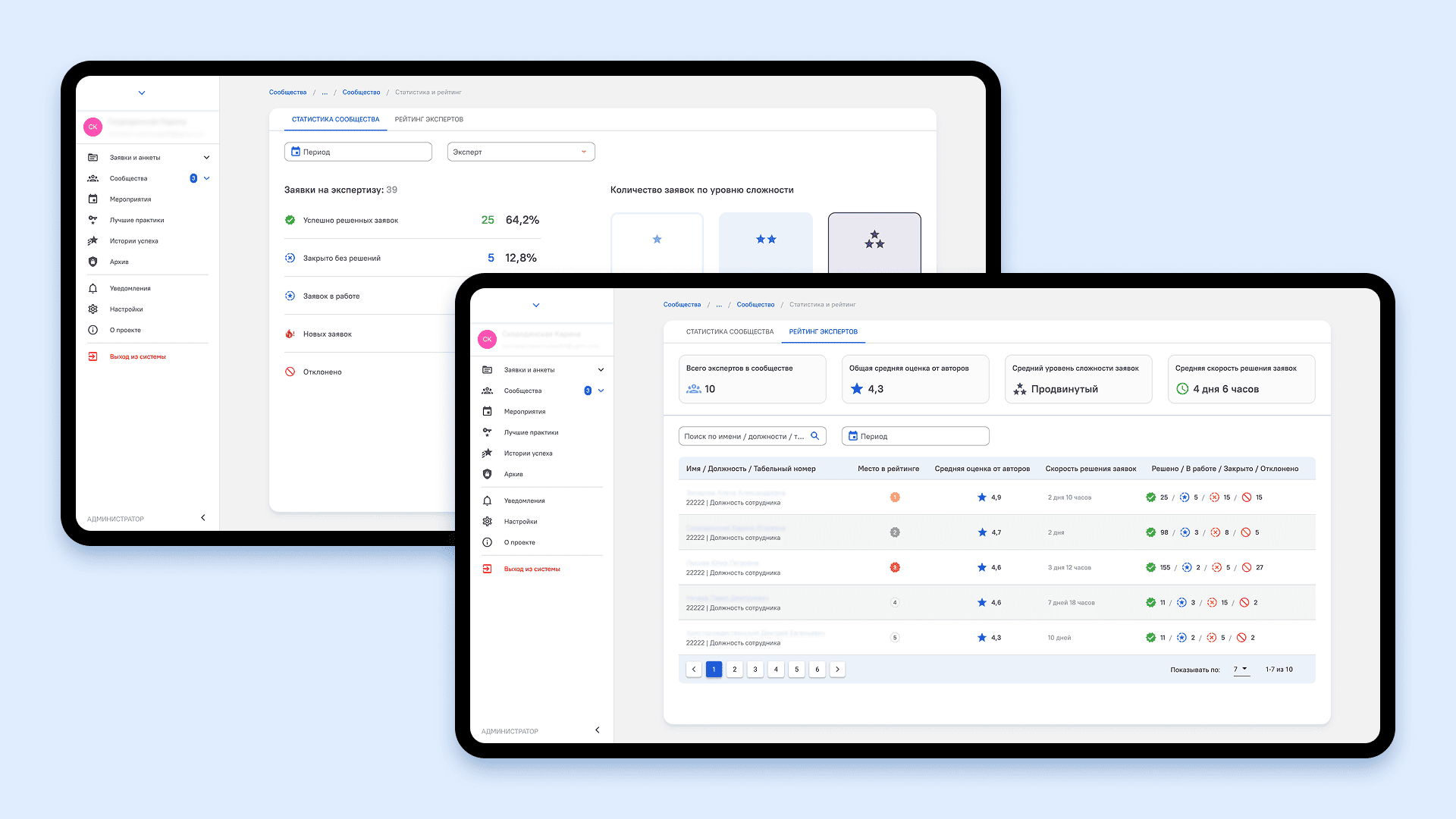
Как внедрить бережливое производство и цифровые инструменты
Разберем по шагам, как внедрить бережливое производство и усилить его с помощью цифровых продуктов.
Шаг 1. Провести диагностику текущих процессов
Перед тем, как что-то менять в процессах, нужно разобраться, где именно теряется время и энергия. Для этого руководители:
- наблюдают за операциями на месте;
- разговаривают с линейными сотрудниками и мастерами;
- фиксируют повторяющиеся действия, задержки и дублирующиеся функции.
На этом этапе часто всплывают такие вещи, которые были приняты, но по факту они не приносят результатов.
Шаг 2. Определить ориентиры
Необходимо определить цели с конкретными и измеримыми результатами. Например:
- сократить время на выполнение ключевых операций;
- снизить количество брака;
- увеличить число реализованных предложений;
- ускорить реакцию на проблемы.
Без таких ориентиров люди не поймут, на что ориентироваться и зачем в компании происходят изменения.
Шаг 3. Подготовить команду и цифровую инфраструктуру
Даже простая система улучшений требует создания ролей и структуры. Что нужно:
- лидер проекта, который отвечает за развитие и продвижение лин-концепции;
- эксперты процессов, которые понимают механику производства;
- цифровая платформа, где фиксируются идеи, задачи и эффекты;
- поддержка руководства, чтобы показывать результаты изменений, защищать сотрудников от саботажа и помогать включаться в организацию улучшений.
Шаг 4. Постепенно масштабировать процессы и продукт
Эффективнее использовать мягкий сценарий: начать с одного участка или команды, а затем — постепенно подключать остальные подразделения и предприятия.
Один из работающих подходов — добровольное использование системы на старте. Сотрудники могут подавать идеи как через сервис, так и по старой схеме. Постепенно площадка становится основным каналом, без жесткого навязывания.
Плюсы такого сценария:
- минимальное сопротивление персонала — никто не чувствует давления;
- возможность отладки процессов — на пилотной группе видны слабые места;
- формирование привычки — система становится естественным инструментом в ежедневной работе.
Именно такой сценарий и применяет наш клиент. Холдинг поэтапно подключает предприятия: сначала — несколько инициативных площадок, затем — остальные. Это дает время на обучение, адаптацию и настройку под бизнес-процессы.
В результате цифровой продукт органично вписывается в работу, а производственные улучшения масштабируются без лишнего напряжения.
Шаг 5. Ориентироваться на результат
Люди включаются в процесс, когда видят, что их усилия что-то меняют. Система работает, если:
- идеи не теряются, а реально доходят до внедрения;
- сотрудники получают обратную связь;
- решения принимаются быстро;
- результат виден в цифрах и отражается на производстве, экономии и сроках.
Такой подход вызывает доверие и запускает постоянное участие в улучшениях.
Подведем итоги
Философия бережливого производства без цифровых инструментов работает только в теории. В реальной компании — с разными площадками, множеством задач и постоянными изменениями — без технологии получается хаос: предложения теряются, решения затягиваются, а сотрудники выгорают от рутины.
Система улучшений строится на трех опорах:
- Методы — понятные принципы, по которым действуют команды.
- Люди — те, кто каждый день видит, как работает процесс, и может его улучшить.
- Технологии — инфраструктура, которая связывает вместе операции и не дает системе развалиться.
Каждая из этих частей важна — вместе они дают устойчивый рост производительности труда. Если идея от мастера доходит до внедрения без проволочек, предложение можно внести за пару кликов и все данные находятся в одном месте — значит, система работает.
0
0
0
Подпишись и будь в курсе новых статей!
Услуги
Читайте также
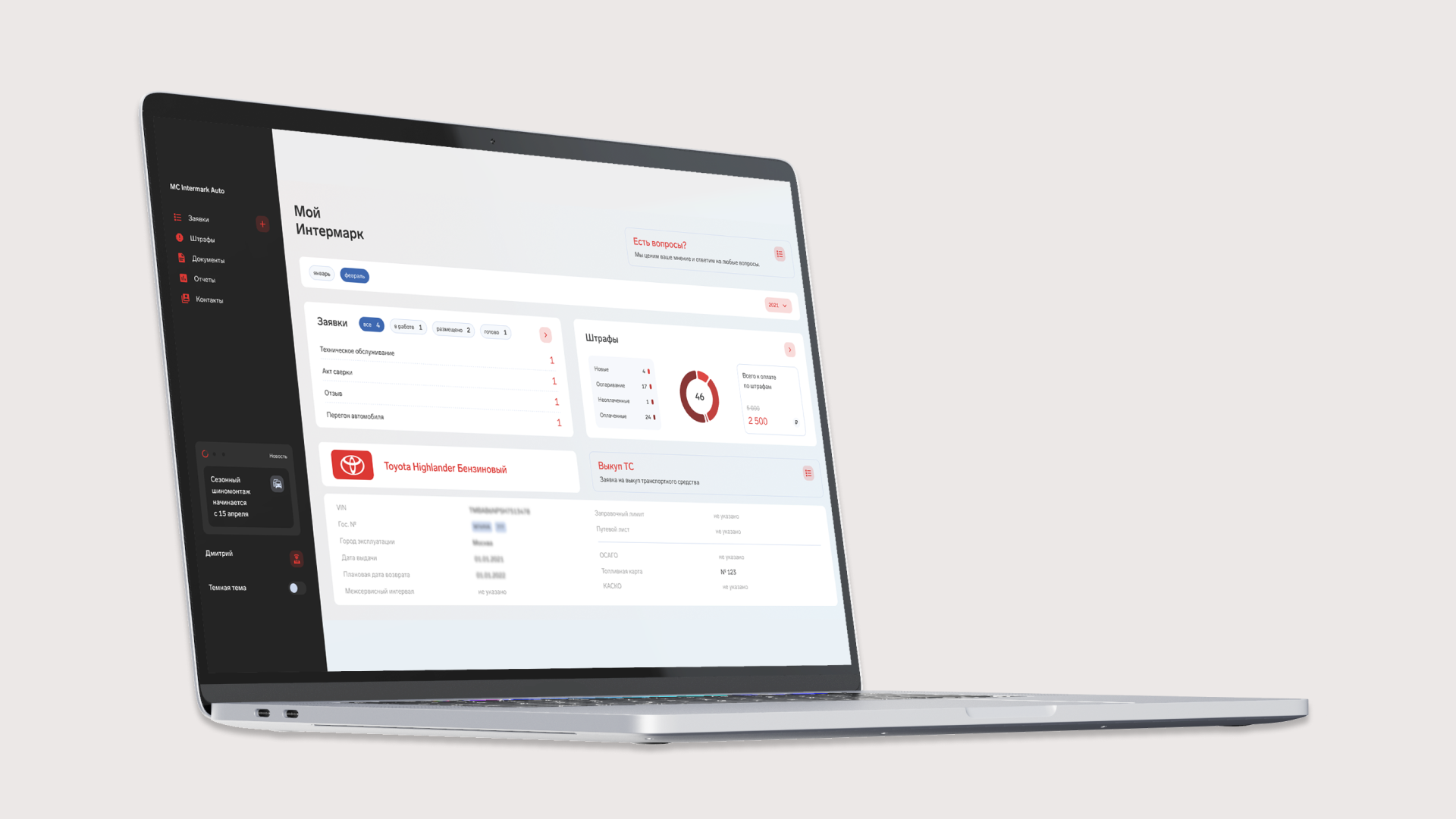
Веб-сервисы: зачем они бизнесу и как с ними работать
Описание принципов работы и применения веб-сервисов в бизнесе.
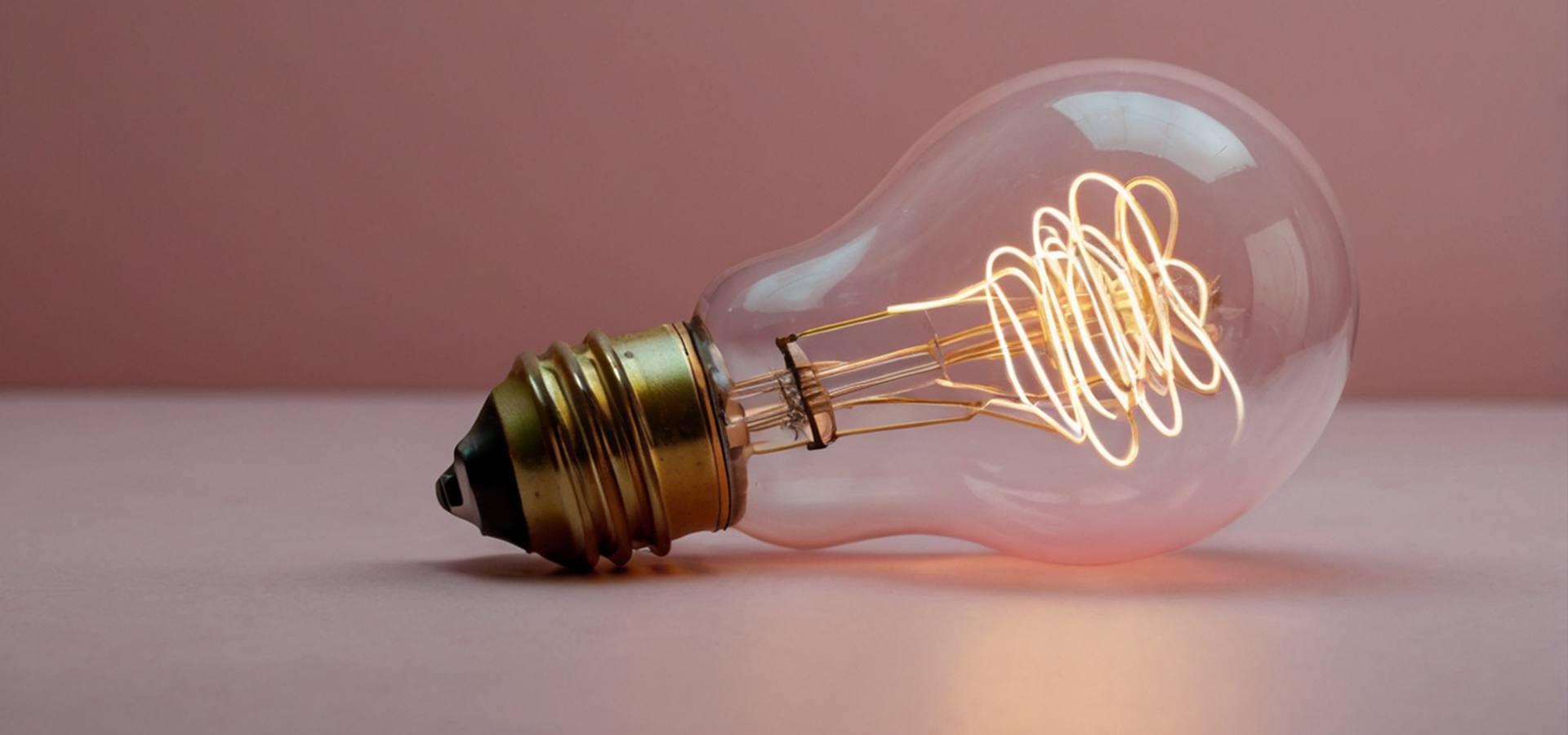
Фабрика идей: как сотрудники помогают бизнесу расти
Когда внедрять фабрику идей и как стимулировать сотрудников предлагать улучшения
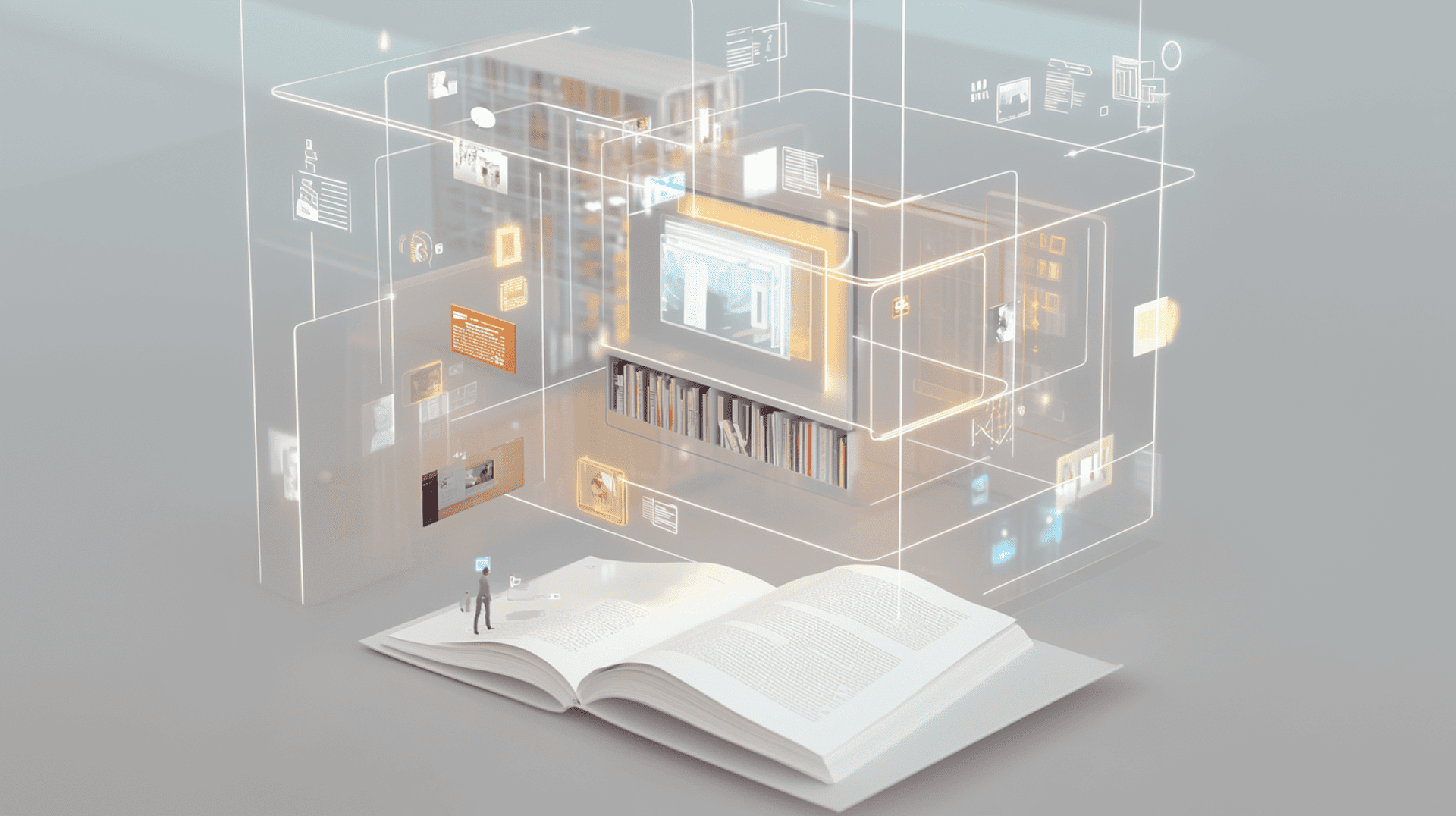
Экспертные сети: зачем бизнесу нужна профессиональная социальная сеть
Рассказываем, как и для каких целей компании внедряют экспертные сети.